PCB压合工序的深度解析
在电子产品的制造过程中,印刷电路板(PCB)作为电子元件之间的连接桥梁,其质量和性能直接关系到整个电子产品的可靠性和稳定性。而在PCB的制造流程中,压合工序无疑是至关重要的一环。本文将深度解析PCB压合工序的原理、工艺流程、关键控制因素、面临的挑战以及解决方案,以期为相关从业者提供全面的参考和指导。
一、PCB压合工序的基本原理
PCB压合的基本原理是通过将多层板材进行加热和加压,实现不同层次之间的粘附和固化,使之成为一体化的多层板。这一过程中,温度和压力的精确控制至关重要,同时还需要考虑材料的膨胀、收缩以及应力的释放等多方面因素。
压合过程的核心在于半固化片(PP胶片)的使用。半固化片是一种由树脂和玻璃纤维组成的片状粘结材料,其中树脂多为热固型高分子聚合物,如环氧树脂。在加热和加压的条件下,树脂软化并流动,填充各层之间的空隙,形成均匀的粘结层。同时,树脂中的大分子链段在压力和温度的作用下发生相互扩散和渗透,形成牢固的化学键合,从而实现多层板的整体粘结。
二、PCB压合的工艺流程
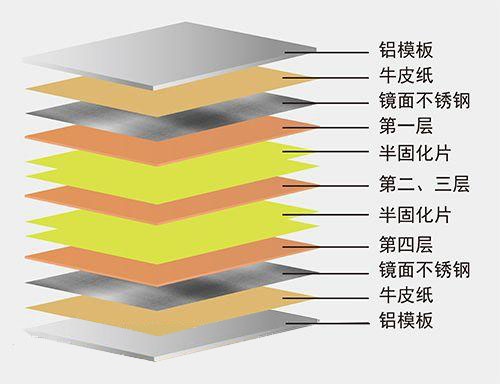
PCB压合的工艺流程包括多个关键步骤,每个步骤都对最终产品的质量有着重要影响。
1. 准备工作
准备工作是压合工序的起点,主要涉及材料的准备和清理。需要准备的材料包括覆铜箔层、半固化片、牛皮纸垫料等,这些材料的表面必须保持无尘无污,以确保压合质量。此外,还需对钢板进行清洁处理,去除表面的胶渍和轻微花痕,为后续的压合操作提供良好的基础。
2. 放板和对位
放板和对位是将多层板按照设计要求进行准确对位的过程。这一步骤要求极高的精确度,因为任何微小的错位都可能导致后续加工时产生层间滑移或电路连接不良。因此,需要使用定位销等工具确保各层之间的精准对齐,为后续的压合操作打下坚实的基础。
3. 预压合
预压合,也称预层压,是在低温、低压下进行初步压合的过程。其主要目的是使层间材料初步结合,为正式压合做准备。预压合过程中会使用预热和低压,以避免层间材料过度流动,同时防止空气和杂质的进入。通过预压合,可以减少正式压合时的调整时间和误差,提高生产效率。
4. 正式压合
正式压合是在高温、高压的环境中进行的关键步骤。在这一阶段,层间材料充分流动并固化,最终形成坚固的多层PCB板。温度和压力需要精确控制,以保证各层材料的完全结合和电性能的稳定。树脂在压力和温度的作用下完全流动并填充各层之间的空隙,形成均匀的粘结层;同时,树脂中的大分子链段发生相互扩散和渗透,形成牢固的化学键合。
5. 冷却与脱模
压合完成后,需要进行冷却降温。待到达一定温度后进行脱模,得到最终的多层PCB成品。冷却过程中,树脂逐渐固化并形成稳定的化学键合。脱模时需小心操作,以避免对多层板造成损伤。
6. 后处理
后处理包括去除多余材料、修整边缘、进行表面处理等步骤。去除多余材料主要是去除压合过程中产生的多余树脂和牛皮纸等;修整边缘则是使用锣机或铣床等工具将多层板的边缘修整齐;表面处理则是根据需要进行电镀、喷锡等操作,以提高多层板的导电性能和焊接性能。
三、PCB压合的关键控制因素
在PCB压合过程中,有多个关键控制因素需要特别注意,以确保压合质量和生产效率。
1. 温度控制
温度是决定树脂流动性和固化过程的重要因素。不同的树脂材料需要不同的压合温度和时间。温度过低会导致树脂流动不充分,无法完全填充各层之间的空隙;温度过高则可能导致树脂过度流动,造成多层板变形或层间短路。因此,需要精确控制压合温度,以确保树脂的流动性和固化过程符合要求。
2. 压力控制
压力需要足够使材料结合,但也不能过大,以防止板材变形。压力的分布要均匀,否则会导致压合不良。在正式压合过程中,需要根据多层板的层数和厚度调整压力大小,以确保各层材料能够紧密粘结在一起。同时,还需注意压力的均匀性,以避免多层板在压合过程中出现局部变形或层间分离。
3. 时间控制
压合时间的长短直接影响固化效果。不同材料和结构的PCB需要不同的压合时间。压合时间过短会导致树脂固化不完全,影响多层板的机械性能和电气性能;压合时间过长则可能导致树脂过度固化,造成多层板脆化或开裂。因此,需要精确控制压合时间,以确保树脂的固化效果符合要求。
4. 材料的选择
不同的材料具有不同的膨胀系数和收缩率,选择合适的材料是压合成功的基础。在选择材料时,需要考虑多层板的使用环境、性能要求以及成本等因素。同时,还需注意材料的匹配性和相容性,以确保多层板在压合过程中能够顺利粘结在一起并形成牢固的结构。
5. 环境控制
压合过程中的环境也会影响最终的压合质量。例如,湿度过高会导致树脂吸收水分,影响固化效果;洁净度不足则可能导致多层板表面污染,影响电气性能和可靠性。因此,需要在压合过程中严格控制环境湿度和洁净度等条件。
四、PCB压合面临的挑战及解决方案
随着电子产品的不断进化,PCB压合技术也面临更加严峻的挑战。这些挑战主要包括多层板的复杂性增加、材料的适配性差异、设备的精度要求提高以及工艺参数的优化等。
1. 多层板的复杂性增加
随着电子产品功能的增加,PCB层数也在增加,多层压合的难度随之上升。多层板的复杂性增加对对位精度和压合均匀性的要求更高。为了应对这一挑战,需要采用高精度的定位设备和压合设备,以确保多层板在压合过程中能够准确对位并形成均匀的粘结层。
2. 材料的适配性差异
不同厂家生产的材料特性不完全相同,需要不断进行适配性测试和工艺调整。为了应对这一挑战,需要加强与材料供应商的合作和沟通,及时了解材料的性能和特点,并根据实际情况进行工艺参数的调整和优化。
3. 设备的精度要求提高
高精密设备的投资成本较高,但对于提高多层板的压合质量和生产效率至关重要。为了应对这一挑战,需要加大对高精度设备的投入和研发力度,提高设备的性能和精度。同时,还需加强对设备的维护和保养工作,确保设备能够长期稳定运行。
4. 工艺参数的优化
工艺参数的优化是提高多层板压合质量和生产效率的关键。需要根据不同产品和生产批次不断调整和优化工艺参数,以确保产品质量的稳定性。例如,可以通过调整压合温度、压力和时间等参数来优化树脂的流动性和固化过程;可以通过改进排版和放板方式来提高多层板的对位精度和压合均匀性。
五、总结与展望
PCB压合是印刷电路板制造过程中至关重要的一环,其质量和效率直接关系到电子产品的可靠性和性能。通过对压合原理、工艺流程及关键控制因素的深入理解,可以更好地优化压合工艺,提高PCB的质量和生产效率。然而,随着电子产品的不断进化,PCB压合技术也面临更加严峻的挑战。
未来,随着科技的不断进步和创新,PCB压合技术也将不断发展和完善。通过持续的技术研发和工艺改进,PCB制造商可以在激烈的市场竞争中脱颖而出,满足客户的高端需求,推动电子产品的不断创新和发展。同时,我们也需要关注环保和可持续发展等方面的要求,推动PCB压合技术向更加绿色、高效的方向发展。
总之,PCB压合是一个复杂而精细的过程,需要我们在实践中不断探索和优化。相信在全体从业者的共同努力下,PCB压合技术一定能够迎来更加美好的明天。
深泽多层电路是一家专业的PCB制造商,致力于高阶HDI、多层PCB、HDI打样、PCB打样、PCB快速打样、高频PCB、高速PCB、FPC、软硬结合板、SMT加工以及PCBA代工代料。他们提供一站式PCB及PCBA制造服务,不仅交期快速,而且价格具有竞争力。他们始终为客户提供高性价比和物美价廉的PCB及PCBA产品。
自2006年成立以来,一直致力于提供高阶HDI、多层PCB、HDI打样、PCB打样、PCB快速打样、高频PCB、高速PCB、FPC、软硬结合板、SMT加工以及PCBA代工代料等一站式制造服务。
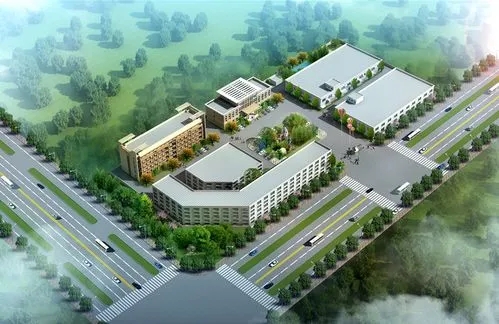