什么是PCB的沉铜工序
引言
印制电路板(Printed Circuit Board,简称PCB)作为现代电子设备的基础组件,其制造过程涉及多个复杂而精细的工序。其中,沉铜工序作为PCB制造中的关键一环,对电路板的导电性、可靠性和性能起着至关重要的作用。本文将详细探讨PCB沉铜工序的原理、流程及其重要性,以期为相关从业人员提供全面的技术参考。
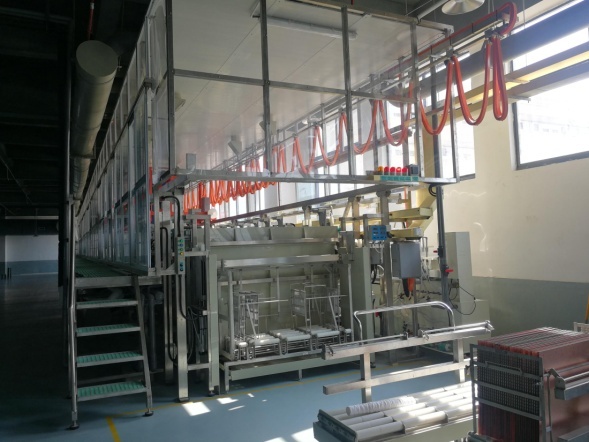
龙门PCB沉铜线
一、PCB的沉铜工序概述
沉铜,也被称为化学镀铜或镀通孔(PTH, Plated-Through-Hole),是PCB制造过程中的一项重要工艺。其主要目的是在已钻孔的不导电孔壁基材上,通过化学方法沉积一层薄薄的化学铜,以作为后续电镀铜的基底。这一工序对于实现PCB板层间的电气连接至关重要,是确保电路板整体性能的关键步骤之一。
二、沉铜工序的原理
沉铜工序的原理基于化学中的置换反应,具体而言是利用甲醛在碱性条件下的还原性来还原被络合的可溶性铜盐,从而在孔壁上沉积一层铜。这一过程可以概括为以下几个关键步骤:
- 前处理:在进行沉铜之前,需要对PCB基板进行一系列前处理,包括去毛刺、碱性除油、粗化(微蚀)等。这些步骤旨在去除基板表面的油污、氧化物和杂质,并增加基材表面的粗糙度,以便后续步骤中胶体钯的吸附。
- 活化:活化是沉铜工序中的关键步骤之一。通过活化处理,可以在基材表面形成一层带有负电荷的胶体钯颗粒。这些胶体钯颗粒作为催化中心,能够诱发后续的化学沉铜反应。活化液的组成和活化条件对沉铜质量有着重要影响。
- 解胶:解胶步骤的目的是去除胶体钯颗粒外面包围的亚锡离子,使胶体颗粒中的钯核暴露出来,以便直接催化启动化学沉铜反应。常用的解胶剂包括氟硼酸等,其选择需根据具体工艺条件进行调整。
- 沉铜:在活化后的基材上,通过加入含有铜离子的溶液和还原剂(如甲醛),可以触发化学沉铜反应。在适宜的温度和pH值条件下,还原剂将溶液中的铜离子还原成金属铜,并沉积在基材表面和孔壁上。沉铜层的厚度和均匀性对后续的电镀和焊接工序有着重要影响。
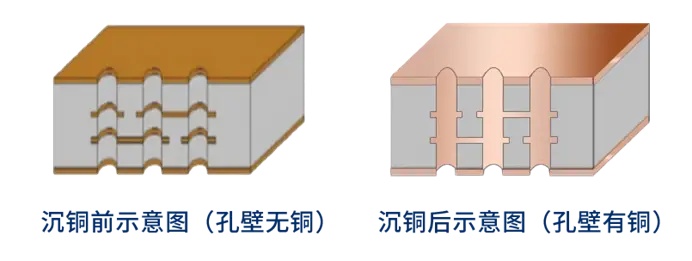
三、沉铜工序的流程
沉铜工序的流程通常包括以下几个关键步骤:
- 去毛刺:在钻孔过程中,孔边和内孔壁容易产生毛刺。这些毛刺不仅会影响后续工序的进行,还可能成为劣质孔金属化的隐患。因此,在沉铜前需要进行去毛刺处理,通常采用机械方式去除孔边和内孔壁的毛刺。
- 碱性除油:除去板面油污、指印、氧化物和孔内粉尘等杂质。同时,对孔壁基材进行极性调整(使孔壁由负电荷调整为正电荷),便于后续工序中胶体钯的吸附。碱性除油体系相比酸性除油体系具有更好的除油效果和电荷调整效果。
- 粗化(微蚀):除去板面的氧化物并粗化板面,以保证后续沉铜层与基材底铜之间良好的结合力。常用的粗化剂包括硫酸双氧水体系和过硫酸盐体系等。粗化过程中需要严格控制槽液的温度、浓度和搅拌速度等参数。
- 预浸:在活化前进行预浸处理,以保护活化剂钯槽避免带入太多的水分及杂质,并提供活化剂所需要的氯离子。预浸液的比重和铜含量等参数需要严格控制。
- 活化:在预浸后的基材上涂覆活化液,使带正电的孔壁有效吸附足够带有负电荷的胶体钯颗粒。活化过程中需要控制活化液的温度、浓度和搅拌速度等参数,以保证活化效果。
- 解胶:去除胶体钯颗粒外面包围的亚锡离子,使胶体颗粒中的钯核暴露出来。解胶过程中需要选择合适的解胶剂并控制其浓度和温度等参数。
- 沉铜:在活化后的基材上加入含有铜离子的溶液和还原剂(如甲醛),触发化学沉铜反应。沉铜过程中需要控制槽液的温度、pH值、铜离子浓度和还原剂浓度等参数,以保证沉铜层的厚度和均匀性。
- 后续处理:沉铜完成后,还需要进行后续处理步骤如清洗、干燥和检测等。这些步骤旨在去除基材表面的残留物并检查沉铜层的质量是否符合要求。
四、沉铜工序的关键影响因素
沉铜工序的质量受到多种因素的影响,以下是一些关键的影响因素:
- 前处理效果:前处理步骤如去毛刺、碱性除油和粗化等的效果直接影响后续沉铜工序的质量。如果前处理不彻底或参数控制不当,可能导致沉铜层与基材之间的结合力差或沉铜层厚度不均匀等问题。
- 活化效果:活化步骤的效果对沉铜层的均匀性和连续性有着重要影响。如果活化不充分或活化液参数控制不当,可能导致沉铜层出现空洞或断裂等问题。
- 沉铜液参数:沉铜液的参数如温度、pH值、铜离子浓度和还原剂浓度等直接影响沉铜层的厚度和均匀性。如果参数控制不当,可能导致沉铜层过薄或过厚、不均匀或出现其他质量问题。
- 操作环境:操作环境如温度、湿度和洁净度等也对沉铜工序的质量有着重要影响。如果操作环境不佳,可能导致沉铜过程中出现污染或质量问题。
五、沉铜工序在PCB制造中的重要性
沉铜工序在PCB制造中扮演着至关重要的角色。其重要性主要体现在以下几个方面:
- 实现层间电气连接:通过沉铜工序,可以在PCB板的不同层之间实现电气连接。这是PCB板实现复杂电路设计和多功能性的基础。
- 提高电路板的可靠性:沉铜层作为电镀铜的基底,其质量和均匀性对电路板的可靠性和耐久性有着重要影响。高质量的沉铜层可以提高电路板的导电性和抗剥离强度,从而延长电路板的使用寿命。
- 降低制造成本:沉铜技术能够替代传统的层间连接方式,实现单层板上的层间连接。这不仅可以降低多层板的制作成本,还可以提高生产效率。
- 提升PCB性能:沉铜工序能够制造出精细的线路和更密集的布线结构,从而提升PCB的集成度和性能。这对于满足现代电子设备对高性能、小型化和轻量化的需求具有重要意义。
六、沉铜工序的发展趋势
随着电子技术的不断发展和PCB制造技术的不断进步,沉铜工序也在不断发展和完善。以下是一些沉铜工序的发展趋势:
- 绿色化生产:随着全球对环保要求的日益严格,绿色化生产已成为PCB制造行业的重要趋势之一。沉铜工序也在逐渐向低能耗、无铅化和环保材料方向发展,以满足环保法规的要求。
- 智能化生产:通过引入智能制造技术如AI、大数据和工业物联网(IIoT)等,可以优化沉铜工序的生产流程和提高资源利用率。这不仅可以提高生产效率和质量稳定性,还可以降低生产成本和环境污染。
- 高精度和细线化:随着电子设备对高性能和小型化需求的不断增加,PCB制造也在向高精度和细线化方向发展。沉铜工序需要不断提高其精度和稳定性以满足这一需求。
- 新材料的应用:随着新材料的不断涌现和应用技术的不断进步,沉铜工序也在不断探索和应用新材料以提高其性能和可靠性。例如采用纳米材料或复合材料等可以提高沉铜层的导电性和抗剥离强度等性能。
七、结论
PCB的沉铜工序作为PCB制造中的一项核心工艺,在实现层间电气连接、提高电路板可靠性和性能等方面发挥着至关重要的作用。通过深入了解沉铜工序的原理、流程及其影响因素等内容,可以更好地掌握这一关键工艺并提高其质量和效率。随着电子技术的不断发展和PCB制造技术的不断进步,沉铜工序也将不断发展和完善以满足日益增长的市场需求和技术挑战。
深泽多层电路是一家专业的PCB制造商,致力于高阶HDI、多层PCB、HDI打样、PCB打样、PCB快速打样、高频PCB、高速PCB、FPC、软硬结合板、SMT加工以及PCBA代工代料。他们提供一站式PCB及PCBA制造服务,不仅交期快速,而且价格具有竞争力。他们始终为客户提供高性价比和物美价廉的PCB及PCBA产品。
自2006年成立以来,一直致力于提供高阶HDI、多层PCB、HDI打样、PCB打样、PCB快速打样、高频PCB、高速PCB、FPC、软硬结合板、SMT加工以及PCBA代工代料等一站式制造服务。
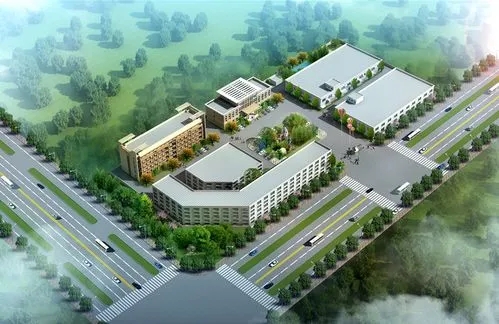