如何预防和改善PCB翘曲度过大
在电子制造业中,PCB(印制电路板)的质量直接关系到电子设备的性能与可靠性,而翘曲度是衡量PCB质量的关键指标之一。翘曲度过大不仅会给生产装配带来诸多难题,还会严重影响电子设备的使用寿命。下面将从PCB翘曲度的定义、影响因素、改善方法及结论四个方面进行详细阐述。
一、什么是PCB的翘曲度
PCB 的翘曲度指的是PCB板在不受外力作用时,其实际平面与理想平面之间的偏离程度,它反映了PCB板的平整性。这种偏离通常是由于PCB内部存在应力,导致板子发生弯曲或扭曲变形。
在行业中,通常采用以下方法来测量PCB的翘曲度:将PCB板放置在一个水平的基准面上,使用高度规或专门的翘曲度测量仪器,测量PCB板上各点与基准面之间的最大距离,然后与PCB板的对角线长度或最长边长度相比,得到的比值即为翘曲度,一般以百分比表示。
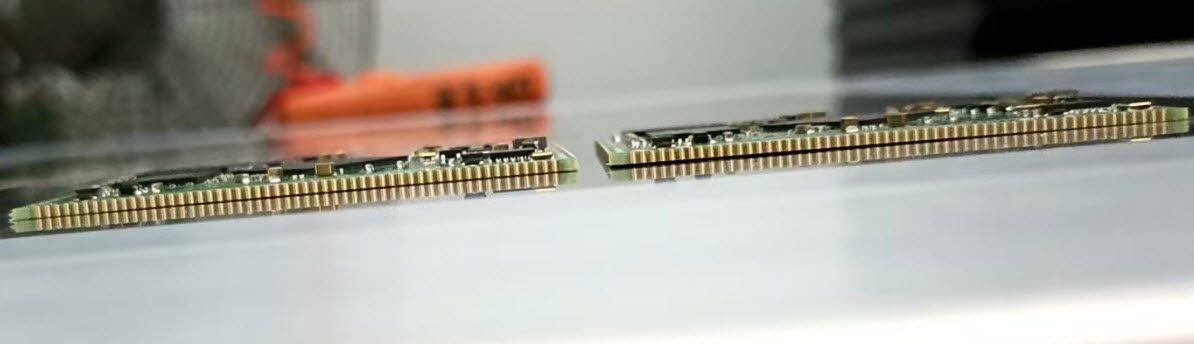
不同应用场景对PCB翘曲度的要求有所不同,通常消费类电子产品中,PCB 的翘曲度要求控制在 0.75% 以内;而在一些高精度的工业设备或航空航天领域,对翘曲度的要求更为严格,可能需要控制在 0.3% 甚至更低。这是因为高精度设备中,电子元件的安装精度要求极高,微小的翘曲都可能导致元件焊接不良、接触不良等问题,进而影响设备的正常运行。
二、影响PCB翘曲度的因素有哪些?
(一)材料因素
材料的性能是影响PCB翘曲度的根本因素,主要体现在基材、覆铜板和辅料三个方面。
基材的物理性能差异会直接导致翘曲。不同基材的热膨胀系数差异明显,当PCB经历温度变化时,热膨胀系数不匹配会使板子各部分的伸缩程度不同,产生内应力,引发翘曲。例如,在高温焊接过程中,若基材热膨胀系数过大,就容易因剧烈膨胀收缩而发生翘曲。
覆铜板的质量对翘曲度影响重大。覆铜板厚度不均匀,会使PCB在加工和使用过程中受力不均,进而导致翘曲;树脂含量不合理,过高会使覆铜板固化后脆性增加,过低则会影响其粘结力,都可能引发翘曲;纤维布作为覆铜板的增强材料,其编织密度不均、张力不一致等问题,会导致覆铜板内部结构应力分布失衡,最终使PCB出现翘曲。
辅料的选用也不容忽视。粘结剂、阻焊剂等辅料与基材的热膨胀系数不匹配时,在温度变化过程中会产生额外应力,导致PCB翘曲。同时,辅料的固化程度、粘结强度等质量问题,也会影响PCB的结构稳定性,间接造成翘曲。
(二)设计因素
PCB 的设计方案在很大程度上决定了其是否容易出现翘曲问题,具体体现在布局、尺寸和结构设计三个方面。
布局设计中,铜箔分布是关键。铜箔在PCB中不仅起到导电作用,其分布状态还会影响板子的应力平衡。若铜箔分布不均匀,在蚀刻、焊接等工艺过程中,不同区域的热量吸收和释放速度不同,会产生不均匀的应力,导致PCB翘曲。例如,大面积铜箔区域与小面积铜箔区域的交界处,往往是应力集中的地方,容易出现翘曲现象。
尺寸设计不合理也会增加翘曲风险。一般来说,PCB 的尺寸越大,其在生产和使用过程中受到温度、外力等因素的影响就越明显,发生翘曲的概率也就越高。此外,PCB 的长宽比例失调,会使板子的结构稳定性下降,在受到外力或温度变化时,容易出现弯曲变形。
结构设计对多层PCB的翘曲度影响尤为显著。多层PCB由多个基板层压而成,若各层的材料选择、厚度设计等不一致,会导致层间应力不平衡,在压合及后续使用过程中产生翘曲。同时,PCB 上的孔径大小、孔的分布密度等结构参数也会影响其结构强度,孔径过大或分布不均会削弱PCB的整体刚性,增加翘曲的可能性。
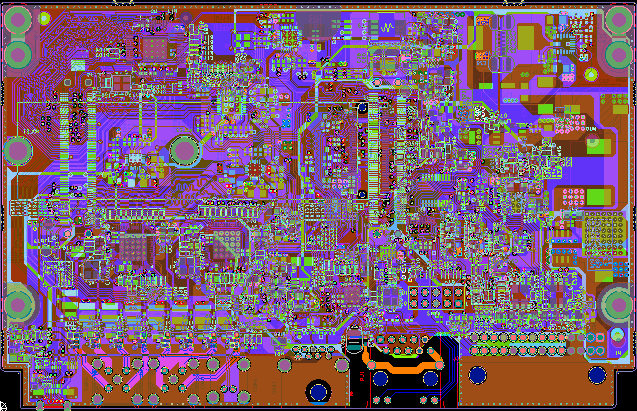
(三)工艺因素
PCB 的生产工艺复杂繁琐,每个工艺环节的操作不当都可能导致翘曲度超标,主要涉及裁剪、压合、蚀刻和焊接等工艺。
裁剪工艺是PCB生产的第一道工序,其质量直接影响后续加工。若裁剪设备精度不足,导致裁剪尺寸偏差过大或裁剪边缘不平整,会使PCB在后续加工过程中受力不均,进而引发翘曲。此外,裁剪过程中若对板材施加的压力过大,会使板材内部产生残余应力,这些应力在后续工艺中释放时,就会导致PCB翘曲。
压合工艺是多层PCB生产中的关键环节,对翘曲度的影响至关重要。压合过程中的温度、压力和时间控制不当,都会导致PCB翘曲。温度过高或升温速度过快,会使基板中的树脂固化反应过于剧烈,产生不均匀的内应力;压力不足或分布不均,会使各层基板之间结合不紧密,存在空隙,影响PCB的平整度;压合时间过短,树脂无法充分固化,而时间过长则可能导致基板材料性能下降,这些都会引发PCB翘曲。
蚀刻工艺中,蚀刻液的浓度、温度和蚀刻时间等参数控制不当,会导致铜箔蚀刻不均匀。部分区域铜箔残留过多,部分区域蚀刻过度,会使PCB表面出现凹凸不平,破坏板子的应力平衡,导致翘曲。同时,蚀刻过程中产生的化学反应会使PCB产生一定的应力,若应力分布不均,也会引发翘曲。
焊接工艺中的高温环境是导致PCB翘曲的重要因素。焊接时,PCB 和电子元件都会因高温而发生热膨胀,若两者的热膨胀系数差异较大,且焊接温度过高或焊接时间过长,会使PCB在冷却过程中产生较大的收缩应力,进而导致翘曲。此外,焊接顺序不合理,使PCB局部区域反复受热,也会破坏其应力平衡,引发翘曲。
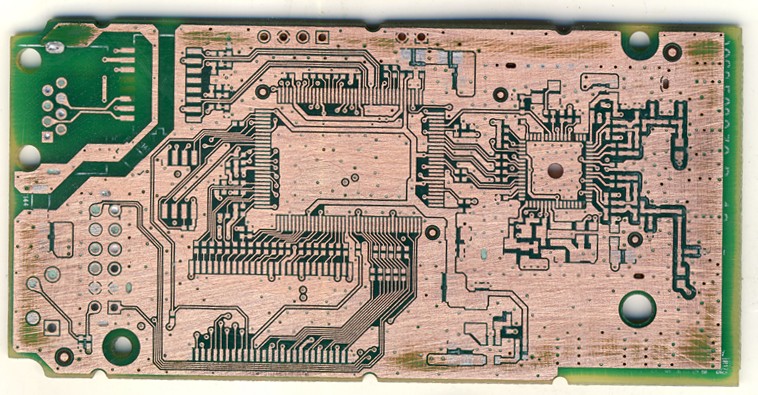
(四)机械与环境因素
PCB 在运输、存储和使用过程中,受到的机械力和环境条件的影响也可能导致翘曲度增大。
机械力作用方面,运输过程中的碰撞、挤压是常见原因。若包装不当,PCB 在运输过程中会与其他物体发生剧烈碰撞,或因堆叠挤压而产生变形。存储过程中,若堆叠方式不合理,如堆叠过高,底层的PCB会承受较大的压力,长期下来就会发生翘曲。在装配过程中,操作人员若操作不当,对PCB施加过大的外力,也会导致其变形翘曲。
环境条件中的温度和湿度变化对PCB翘曲度影响显著。温度的剧烈变化会使PCB材料发生热胀冷缩,若材料的热膨胀系数不一致或温度分布不均,就会产生应力,导致翘曲。湿度过高会使PCB材料吸湿膨胀,湿度过低则会使材料干燥收缩,频繁的湿度变化会使PCB反复发生膨胀和收缩,逐渐积累应力,最终导致翘曲。
(五)其他因素
除了上述主要因素外,设备精度、人员操作和质量检测等因素也会对PCB的翘曲度产生影响。
设备精度是保证PCB生产质量的基础。若生产设备如钻孔机、印刷机等的精度不足,会导致PCB加工尺寸偏差、图形转移不准确等问题,进而影响PCB的应力分布,引发翘曲。例如,钻孔机精度不够会使孔位偏差,导致PCB在装配过程中受力不均,增加翘曲风险。
人员操作的规范性直接影响工艺参数的控制。操作人员若对工艺要求不熟悉,在生产过程中不能准确控制温度、压力、时间等关键参数,会导致工艺不稳定,进而使PCB产生翘曲。同时,操作人员的责任心不强,在操作过程中疏忽大意,如未及时清理设备上的杂物、未正确放置板材等,也会影响PCB的加工质量,增加翘曲的可能性。
质量检测环节的疏漏会使翘曲度超标的PCB流入后续环节。若检测设备精度不足、检测方法不合理或检测人员责任心不强,无法及时发现PCB的翘曲问题,会导致不合格产品进入装配阶段,不仅影响装配效率,还会给电子设备的质量埋下隐患。
三、如何改善PCB翘曲度过大
针对PCB翘曲度过大的问题,需要从材料选择、设计优化、工艺改进、机械与环境控制以及其他管理措施等多个方面入手,采取综合的改善措施。
(一)材料选择优化
在材料选择上,要严格把控基材质量。根据PCB的使用环境和性能要求,选择热膨胀系数、弹性模量等物理性能匹配的基材。优先选用行业内口碑好、质量稳定的供应商,并要求供应商提供详细的材料性能报告。同时,加强对基材的进货检验,对每批次基材进行热膨胀系数、厚度均匀性等关键指标的检测,确保其符合生产要求。
覆铜板的选择要注重质量。选择厚度均匀、树脂含量适中、纤维布编织平整的覆铜板,以减少因覆铜板质量问题导致的翘曲。在采购覆铜板时,要对其进行严格的质量检测,包括外观检查、厚度测量、树脂含量测定等,杜绝不合格的覆铜板进入生产环节。
辅料的选用要与基材相匹配。在选择粘结剂、阻焊剂等辅料时,要确保其热膨胀系数、固化特性等与基材相适应,以减少因辅料与基材不匹配产生的应力。同时,要选择质量可靠的辅料产品,并对其进行粘结强度、固化程度等性能测试,保证辅料质量符合生产要求。
(二)设计方案改进
优化布局设计,确保铜箔分布均匀。在进行PCB布局设计时,要合理规划铜箔的分布,避免出现大面积铜箔聚集或铜箔分布严重不均的情况。对于大面积铜箔区域,可以采用网格状、条纹状等设计方式,以分散应力,减少翘曲风险。同时,在铜箔分布不均匀的区域,可通过增加平衡铜箔等方式,调整应力分布。
合理设计PCB尺寸。在满足电子设备功能要求的前提下,尽量减小PCB的尺寸,以降低翘曲的可能性。对于必须采用大尺寸PCB的情况,要合理设计其长宽比例,并适当增加边框宽度、设置加强筋等,提高PCB的结构稳定性。
改进多层PCB的结构设计。在多层PCB设计中,要保证各层的材料性能和厚度设计对称,以减少层间应力。合理设计孔径大小和分布,避免在局部区域集中布置过多大孔径,保证PCB的结构强度均匀。此外,可在PCB的适当位置设置加强结构,如增加金属支架安装位等,提高PCB的抗翘曲能力。
(三)生产工艺优化
优化裁剪工艺,减少机械应力。选用高精度的裁剪设备,并定期对设备进行校准和维护,确保裁剪尺寸精度和裁剪边缘质量。在裁剪过程中,合理控制裁剪速度和压力,避免产生过大的机械应力。裁剪完成后,对PCB进行应力释放处理,如在适当温度下进行烘烤,以消除残余应力。
严格控制压合工艺参数。根据多层PCB的材料和结构特点,制定合理的压合工艺曲线,精确控制压合温度、压力和时间。在压合过程中,确保温度均匀分布,压力稳定且均匀施加,保证各层基板充分结合。压合前,对基板进行预处理,如清洁表面、去除氧化层等,提高压合质量,减少层间应力。
优化蚀刻工艺,保证蚀刻均匀。严格控制蚀刻液的浓度、温度和蚀刻时间,定期对蚀刻液进行检测和调整,确保其性能稳定。改进蚀刻设备的喷淋系统,保证PCB表面与蚀刻液接触均匀,提高蚀刻均匀性。蚀刻完成后,及时对PCB进行清洗和干燥,避免残留蚀刻液对PCB造成腐蚀和应力影响。
规范焊接工艺操作。根据PCB和电子元件的特性,选择合适的焊接温度和时间,避免焊接温度过高或焊接时间过长。优化焊接顺序,避免PCB局部区域长时间受热,减少应力集中。焊接完成后,让PCB缓慢冷却,以减少因温度骤变产生的应力。
(四)机械与环境控制
加强运输和存储过程中的管理。在运输PCB时,采用合适的包装材料,如防静电托盘、泡沫缓冲材料等,避免PCB在运输过程中受到碰撞和挤压。存储PCB时,要采用平整的货架,合理控制堆叠高度,避免受力不均。对于大型 PCB,可采用悬挂式存储方式,减少应力积累。
控制使用环境的温湿度。在PCB的存储和使用环境中,安装温湿度控制系统,将温度控制在 15-30℃,相对湿度控制在 40%-60%。避免PCB长时间处于极端温度或湿度环境中,对于在特殊环境中使用的 PCB,要采取相应的防护措施,如高温环境下使用的PCB可增加散热装置,潮湿环境下使用的PCB可涂刷防潮涂层。
(五)其他管理措施
提高设备精度和维护水平。定期对生产设备进行校准和维护,确保设备的精度符合生产要求。建立设备维护保养计划,对关键设备进行重点维护,及时发现和排除设备故障,保证设备正常运行。
加强人员培训和管理。定期对操作人员进行业务培训,提高其对工艺参数的控制能力和操作规范性。建立健全的岗位责任制,明确操作人员的职责,加强对操作人员的考核和监督,提高其责任心。
完善质量检测体系。采用高精度的翘曲度检测设备,如激光测平仪等,提高检测精度。制定严格的检测标准和流程,对PCB生产的各个环节进行全面检测,及时发现翘曲度超标的产品,并对其进行分析和处理。同时,建立质量追溯体系,对不合格产品的原因进行追溯,采取纠正和预防措施,避免类似问题再次发生。
四、结论
PCB 翘曲度过大是电子制造业中一个不容忽视的问题,它会对电子设备的生产装配、性能和可靠性产生严重影响。其产生的原因涉及材料、设计、工艺、机械与环境及其他多个方面,是多种因素共同作用的结果。
为了有效预防和改善PCB翘曲度过大的问题,需要从源头抓起,在材料选择上严格把关,确保材料性能匹配、质量可靠;在设计环节进行优化,合理布局、设计尺寸和结构;在生产工艺过程中,精确控制各工艺参数,规范操作;在运输、存储和使用过程中,加强机械力和环境因素的控制;同时,提高设备精度、加强人员培训和完善质量检测体系也至关重要。 通过采取上述综合措施,能够显著降低PCB翘曲度超标的概率,提高PCB的质量和可靠性,从而为电子设备的稳定运行提供有力保障,推动电子制造业的健康发展。在未来的生产实践中,还需要不断探索和创新,结合新的技术和方法,进一步提升PCB的质量控制水平,以适应电子设备不断升级的需求。