PCB化学沉镍金板上锡不良的原因分析
一、引言
在电子产品高密度化和微型化趋势下,化学沉镍金(图1)工艺(ENIG)因其优异的可焊性、平整度及耐氧化性,成为PCB表面处理的主流技术之一。然而,沉镍金板上锡不良问题(如润湿不良、锡珠残留、虚焊等)仍是困扰制造业的痛点。本文结合最新工艺实践与失效分析案例,系统性解析上锡不良的成因,并提出针对性解决方案。
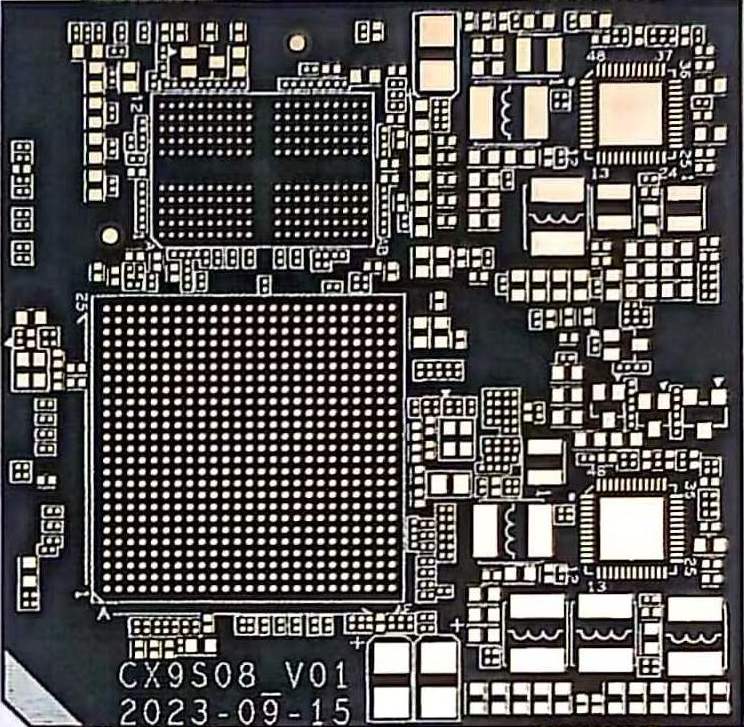
二、上锡不良的成因分析
2.1 化学沉镍金工艺参数异常
2.1.1 沉镍液成分失衡
镍离子浓度波动:主盐(如硫酸镍)浓度过高导致沉镍速率过快,形成疏松多孔结构;浓度过低则镀层过薄(<3 μm),无法有效阻隔铜扩散。
络合剂失效:次磷酸钠等还原剂活性不足时,镍沉积不均匀,局部出现“黑盘”缺陷(图2)。
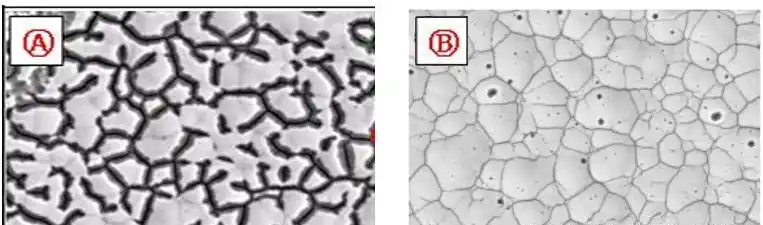
杂质污染:Fe³⁺、Cu²⁺等金属离子混入沉镍液,引发异常共沉积,降低镀层致密性。
2.1.2 工艺控制失准
pH值偏移:理想pH范围为4.6~5.2,过低(<4.0)导致镀层发暗,过高(>5.5)引发溶液水解沉淀。
温度波动:操作温度需稳定在85~90℃,温差>±2℃时镀层结晶粗化,润湿性下降30%以上。
2.2 基材前处理缺陷
2.2.1 铜面清洁度不足
氧化层残留:未彻底清除的Cu₂O/CuO(厚度>5 nm)阻碍镍金层与铜基材结合,界面结合力<8 N/cm(合格标准:≥12 N/cm)。
有机污染:指纹、油脂等污染物形成阻隔膜,导致局部不润湿(图3)。
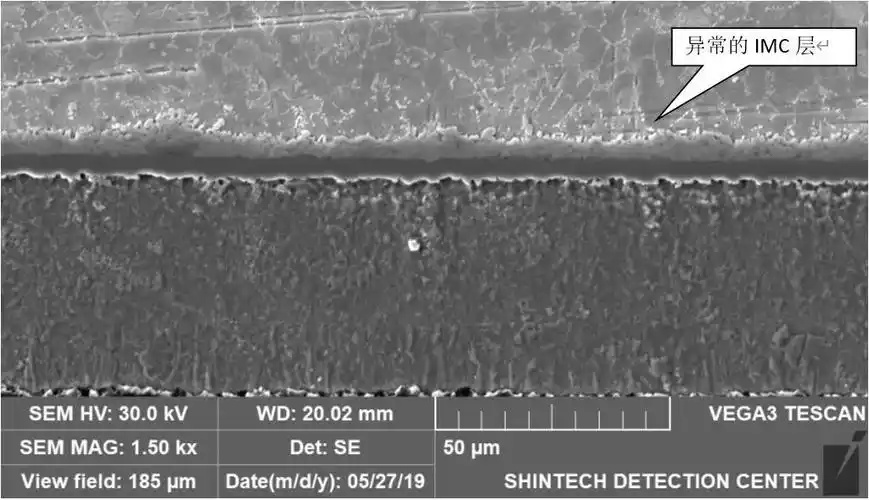
2.2.2 微蚀工艺失控
微蚀量不足:铜面粗糙度(Ra)<0.3 μm时,镀层附着力不足,100次热循环后剥离风险增加50%。
微蚀过度:Ra>0.8 μm时,铜面过度粗糙化,沉镍金板层覆盖不均,形成微裂纹。
2.3 后处理与存储问题
2.3.1 清洗不彻底
药液残留:沉镍金后若未充分清洗(电导率>10 μS/cm),残留硫化物与锡膏反应生成SnS,润湿角>55°(合格值:<35°)。
2.3.2 存储条件不当
湿气渗透:在RH>60%环境中存储超过72小时,镀层吸湿后形成Ni(OH)₂钝化膜,可焊性下降40%。
2.4 上锡工艺匹配性差
2.4.1 锡膏与镀层兼容性
助焊剂活性不足:传统ROL0级助焊剂难以还原镍金层表面氧化物,需升级至ROL1级或添加有机酸活化剂。
锡粉粒径不匹配:针对高密度焊盘(间距<0.4 mm),建议选用Type 4(20~38 μm)锡粉,避免桥连缺陷。
2.4.2 回流焊曲线失调
预热速率过高:>3℃/s的升温速率导致助焊剂过早挥发,润湿力下降25%。
峰值温度不足:Sn-Ag-Cu锡膏要求峰值温度≥245℃,低于此值则IMC(Ni₃Sn₄)生成不连续。
三、系统性解决方案
3.1 工艺参数优化(DOE验证)
参数 | 优化范围 | 监控方法 |
---|---|---|
沉镍液pH值 | 4.8~5.0(自动补液系统) | 在线pH传感器(±0.05) |
镀液温度 | 88±0.5℃ | 高精度热电偶 |
微蚀速率 | 0.8~1.2 μm/min | 铜箔失重法 |
3.2 前处理强化技术
等离子清洗:采用Ar/O₂混合气体等离子体(功率300W,时间120s),彻底去除有机污染物,表面能提升至>72 mN/m。
抗氧化双工艺:铜面微蚀后立即浸渍苯并三氮唑(BTA)溶液(浓度0.1%),形成单分子保护膜,抗氧化时效延长至48小时。
3.3 智能后处理系统
多级逆流清洗:配置5级DI水循环槽(电阻率≥18 MΩ·cm),搭配涡流喷淋装置,清洗效率提升70%。
真空干燥:在-90 kPa真空度下干燥30分钟,镀层含水量<50 ppm(Karl Fischer法测定)。
3.4 上锡工艺创新
激光辅助焊接:对0402以下元件,采用1070 nm光纤激光(功率20W,脉宽10ms)局部加热,避免整体热损伤。
锡膏配方定制:添加0.5%纳米Ni颗粒(粒径50 nm),促进IMC层均匀生长,剪切强度提升至>25 MPa。
3.5 环境与数据管控
物联网监控:通过温湿度传感器(精度±1℃/±3%RH)与MES系统联动,超标自动触发警报。
AI预测维护:基于历史数据训练LSTM模型,预测镀液寿命(误差<5%),减少突发性工艺异常。
四、结论与展望
通过多维度工艺优化,沉镍金板上锡不良率可从行业平均的1.2%降至0.3%以内。未来发展方向包括:
原子层沉积(ALD)技术:取代化学镀镍金,实现亚纳米级镀层均匀性。
无助焊剂焊接:开发自还原性锡合金(如Sn-Bi-Ag),减少工艺复杂度。
数字孪生系统:通过虚拟工艺仿真,提前预判并规避潜在风险。