PCB可制造性分析深度探讨
PCB DFM分析的意义
印刷电路板(PCB)作为现代电子设备中不可或缺的核心组件,其制造过程复杂且精细,涉及到众多因素的考量与优化。PCB可制造分析(DFM,Design for Manufacturability)作为一种前瞻性的设计理念,旨在通过细致的规划与分析,确保PCB在制造过程中能够高效、可靠地生产出符合质量标准的产品。本文将深入探讨PCB可制造分析的重要性、关键影响因素及其在实际应用中的具体操作,以期为PCB设计与制造领域提供有价值的参考。
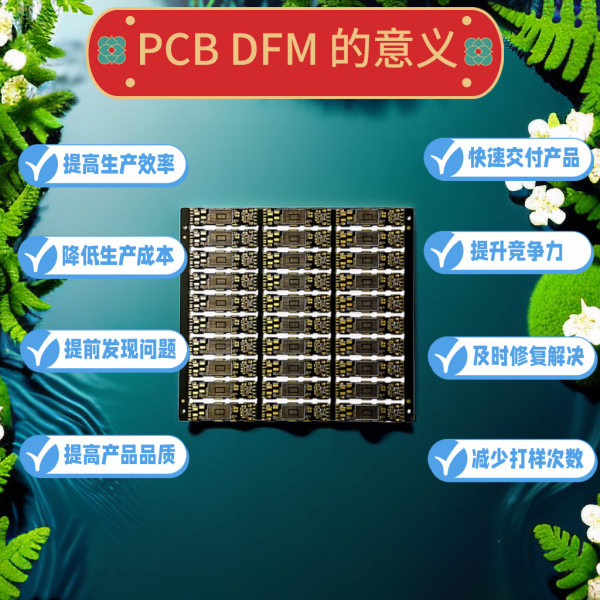
一、PCB可制造分析的重要性
1、提高产品质量
在PCB的设计阶段,潜在的问题可能如暗流般潜伏,若不及时发现并解决,将在后续的制造过程中引发一系列的质量问题。PCB可制造分析正是通过模拟实际的制造流程,对设计进行全方位的审视与评估,从而提前识别并规避可能存在的缺陷。这一过程包括但不限于对导线布局、元件间距、热管理、信号完整性等方面的细致检查。通过及时的修正与优化,可以确保最终生产出的PCB产品符合既定的质量标准,避免因设计缺陷而导致的返工或报废,从而显著提升产品质量。
2、提高生产效率
PCB可制造分析不仅关注产品质量,还致力于提高生产效率,降低生产成本。通过对生产流程的深入分析,可以识别出瓶颈环节,并采取相应的优化措施,如调整工艺顺序、改进设备配置、优化材料利用率等。这些优化措施能够显著减少材料消耗、缩短加工时间、降低废品率,从而在不牺牲产品质量的前提下,实现生产成本的有效控制。此外,PCB可制造分析还有助于优化供应链管理,确保原材料和设备的及时供应,减少因供应链中断而导致的生产延误,进一步提升了整体生产效率。
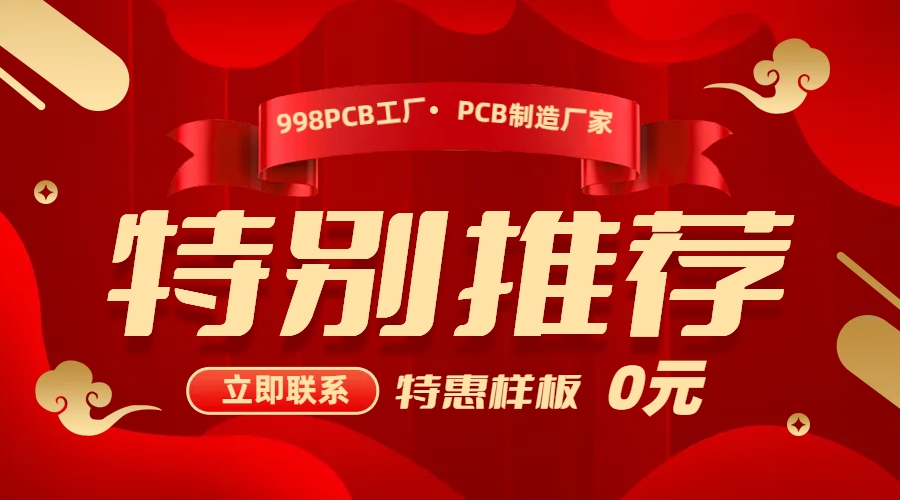
二、PCB可制造分析的关键因素
1、材料选择
材料是PCB制造的基础,其选择直接关系到产品的性能、可靠性和成本。在PCB可制造分析中,材料的选择需综合考虑多个因素:首先,材料应具备可靠的电气性能和物理强度,以满足产品设计的需求;其次,材料应易于加工,以减少制造过程中的损耗和难度;再者,材料的环保性也是不可忽视的因素,随着全球对环保意识的提升,选择符合环保标准的材料已成为行业趋势。此外,材料供应商的可靠性和成本效益也是选择材料时需要考虑的关键因素。通过综合评估这些因素,可以选出最适合特定应用场景的材料,为后续的制造过程奠定坚实的基础。
2、设计规则
设计规则是PCB制造过程中的重要指导原则,它们规定了导线宽度、间距、层数、过孔大小等关键参数。这些参数的合理设定对于确保PCB的可制造性至关重要。在PCB可制造分析中,应严格遵守既定的设计规则,通过模拟和验证,确保设计符合制造要求。同时,还可以根据实际制造能力和需求,对设计规则进行微调,以进一步提高制造效率和降低成本。例如,通过优化导线布局和间距,可以减少制造过程中的短路和断路风险;通过合理设置层数和过孔大小,可以平衡制造成本和信号完整性需求。
3、制造工艺
制造工艺是PCB制造过程中的核心环节,其稳定性和可靠性直接关系到产品的质量和性能。在PCB可制造分析中,需要对制造工艺进行全面而细致的评估。这包括但不限于层压工艺的稳定性、钻孔精度和效率、镀铜层的均匀性和附着力、蚀刻过程的精度和可控性等。通过优化制造工艺参数,如温度、压力、时间等,可以确保制造过程的稳定性和一致性,从而提高产品质量和生产效率。此外,还可以引入先进的制造工艺和技术,如激光钻孔、化学镀铜等,以进一步提升制造水平和竞争力。
4、质量控制
质量控制是PCB制造过程中的最后一道防线,也是确保产品质量的关键环节。在PCB可制造分析中,应建立完善的质量控制体系,包括原材料检验、过程控制、成品检验等各个环节。通过定期对原材料、半成品和成品进行质量检测和分析,可以及时发现并解决潜在的质量问题。同时,还需要对生产设备进行定期的维护和校准,确保其处于良好的工作状态,以减少因设备故障而导致的质量问题。此外,还可以引入先进的质量管理工具和技术,如六西格玛、统计过程控制等,以进一步提高质量控制水平。
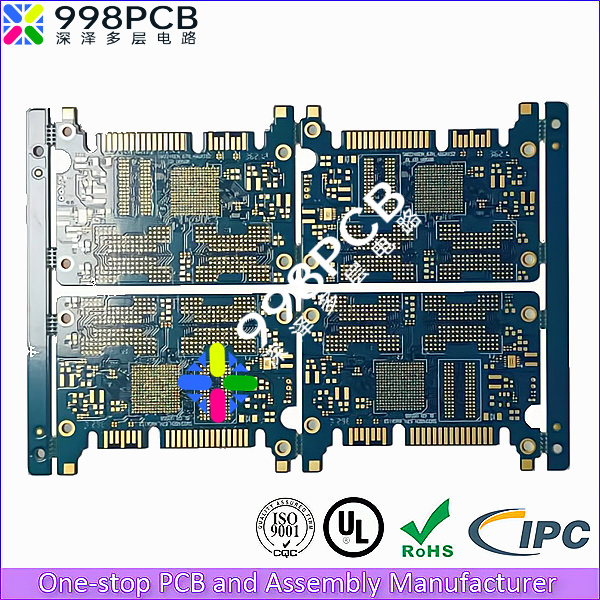
固态硬盘pcb
层数:6层
板材: FR4 Tg170
板厚: 1.0mm
拼板尺寸:122.75*84mm/4
外层铜厚: 1 OZ
内层铜厚: 1OZ
最小通孔: 0.20mm
线宽线距: 3/3mil
最小BGA: 0.25mml
表面处理: 沉金1-2U”
6层固态硬盘PCB,SM2246EN方案,主要用于工业电脑、工控设备,服务器、高稳定存储设备等产品。
三、PCB可制造分析——电子产品制造的基石
综上所述,PCB可制造分析在电子产品制造中扮演着举足轻重的角色。它不仅有助于提高产品质量和生产效率,降低生产成本,还是实现电子产品创新和高性能的关键。通过深入分析材料选择、设计规则、制造工艺和质量控制等关键因素,可以优化生产流程,提升制造水平,从而满足市场对高质量、高效率电子产品的需求。因此,在电子产品设计和制造过程中,应高度重视PCB可制造分析的应用,将其作为提升产品竞争力的有力武器。只有这样,才能在激烈的市场竞争中立于不败之地,推动电子产品制造业的持续健康发展。