PCB黑孔工艺与沉铜工艺的区别
在印制电路板(PCB)制造领域,孔金属化工艺是决定电路连通性与可靠性的核心环节。随着电子设备向高密度、高频化发展,传统沉铜工艺与新兴黑孔工艺正以不同技术路径推动行业进步。本文将从工艺原理、流程差异、性能对比、应用场景及未来趋势等维度,深度剖析PCB黑孔工艺与沉铜工艺这两种孔金属化技术的核心特质,为PCB从业者及行业观察者提供全面参考。
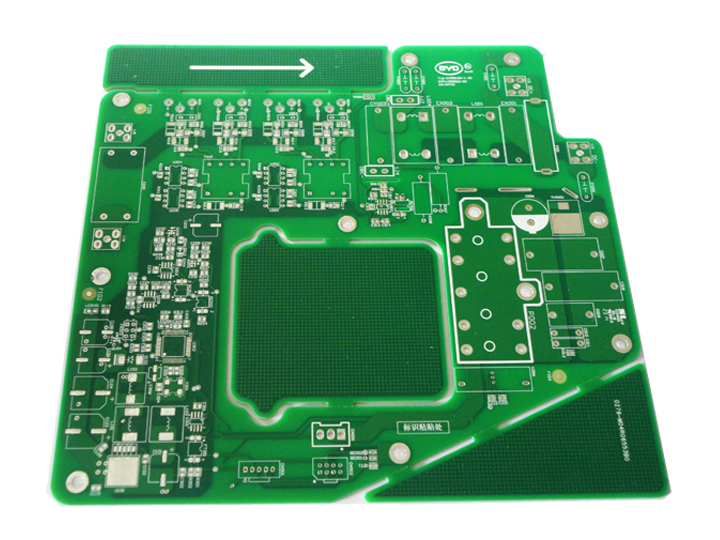
一、工艺原理:PCB黑孔工艺与沉铜工艺技术根基差异
(一)沉铜工艺:化学镀铜的经典范式
沉铜工艺,即化学镀铜(Electroless Plating),其技术原理基于氧化还原反应——通过甲醛等还原剂将铜离子(Cu²⁺)还原为金属铜(Cu),并在催化剂作用下于PCB通孔孔壁有序沉积,形成连续导电层。这一过程类似 “化学电镀”,无需外部电源,仅依靠化学反应自发进行,最终生成的铜层厚度通常控制在0.5-3μm,为后续电镀铜提供导电基底。
核心技术优势:
- 卓越导电性能:纯铜层电阻率低至 1.7μΩ・cm,可满足高频高速电路(如5G基站、服务器主板)的低损耗信号传输需求;
- 厚度灵活可调:通过控制药水浓度与反应时间,沉铜层厚度可在0.2-5μm范围内精准调控,适配不同层数与孔径的PCB设计;
- 工艺高度成熟:历经半个世纪发展,沉铜工艺已形成标准化操作流程,在多层板(≥10 层)、HDI板等复杂结构中表现出极高的可靠性,不良率可控制在0.1%以下。
技术痛点与挑战:
- 环保压力突出:沉铜药水含甲醛、氰化物等有害物质,废水处理需投入专用设备(如化学沉淀槽、RO膜系统),单吨废水处理成本达80-120元;
- 生产成本高昂:生产线设备投资超500万元,药水更换频繁(通常7-10天需更新),单平米生产成本较黑孔工艺高 20%-30%;
- 流程耗时较长:从钻孔到完成沉铜需4-6小时,在小批量打样场景中交期优势不足。
(二)黑孔工艺:物理吸附的创新突破
黑孔工艺,又称 “直接电镀技术”,其原理颠覆了传统化学沉积模式 —— 通过物理手段将碳粉与树脂混合的导电胶粒(粒径约0.1-1μm)吸附于孔壁,形成导电膜。具体流程中,碳粉胶体在静电作用下均匀附着,经固化后形成1-2μm的导电层,替代沉铜工艺中的铜层作为电镀基底。
革新性优势体现:
- 环保性能跃升:不含甲醛、重金属等有害物质,药水成分以碳粉、水溶性树脂为主,废水COD值仅为沉铜工艺的 1/5,处理成本降低 60%;
- 生产效率翻倍:流程简化为 5-6 步(较沉铜减少 40% 环节),生产周期缩短至 2-3 小时,单日产能提升 100%,尤其适合小批量、多品种订单;
- 成本显著优化:设备投资仅为沉铜工艺的 1/3(约150-200万元),能耗降低30%,长期运营成本可节省40%以上。
现存技术瓶颈:
- 导电性能短板:碳粉膜电阻率约5-8μΩ・cm(是铜的3-5倍),在高频(>10GHz)信号传输中损耗较大,限制其在高端领域应用;
- 工艺稳定性待提升:处理纵横比>8:1的深孔时,碳粉均匀性控制难度大,可能导致孔壁镀层断裂,目前主要适用于双面板及简单4层板;
- 应用场景受限:在HDI、高频高速PCB(如毫米波雷达板)中尚无成熟案例,市场渗透率不足20%。
二、流程对比:复杂化学链与极简物理流的效率博弈
(一)沉铜工艺流程:精密化学调控的典型范式
关键控制点:药水温度、pH值、金属离子浓度需实时监测,偏差超过±5%即可能导致镀层空洞或结合力不足。
(二)黑孔工艺流程:物理吸附的极简主义实践
1. **钻孔**:与沉铜工艺同款设备,孔径要求一致;
2. **清洁整孔**:弱碱性溶液(pH8-9)去除孔壁碎屑,常温处理;
3. **黑孔化处理**:碳粉胶体通过喷淋或浸泡附着于孔壁,静电吸附时间约30秒;
4. **微蚀处理**:稀硫酸溶液去除表面多余碳粉,增强电镀结合力;
5. **电镀铜**:与沉铜工艺相同,完成孔壁与板面铜层加厚。
技术优势:省去膨胀、去钻污、活化等化学步骤,无需高温槽体,能耗降低 50%,人工成本减少 30%。
三、性能与成本对比:多维指标下的技术分野
(一)核心性能参数对比
指标 | 沉铜工艺 | 黑孔工艺 |
电阻率(μΩ・cm) | 1.7-2.0 | 5.0-8.0 |
镀层结合力(N/cm) | ≥50 | ≥30 |
耐温度冲击(℃) | -55 至 + 125(1000 次循环无脱落) | -40 至 + 100(500 次循环轻微脱落) |
深孔处理能力(纵横比) | ≥10:1 | ≤8:1 |
高频损耗(10GHz) | <0.5dB/in | 0.8-1.2dB/in |
(二)成本结构分析(以1000平米双面板为例)
成本项 | 沉铜工艺(万元) | 黑孔工艺(万元) | 差异率 |
设备折旧 | 20(5 年分摊) | 8(5 年分摊) | -60% |
药水耗材 | 15(每月更换) | 5(季度更换) | -67% |
废水处理 | 8 | 3 | -62.5% |
能耗(电力 + 水) | 6 | 3 | -50% |
人工成本 | 4 | 2 | -50% |
合计 | 53 | 21 | -60.4% |
四、应用场景:高端制造与绿色生产的市场分化
(一)沉铜工艺:高端PCB的不可替代之选
1. 5G与通信领域
在5G基站AAU(有源天线单元)PCB中,信号频率达28GHz以上,要求孔壁镀层具有极低的信号损耗。沉铜工艺沉积的纯铜层可将10GHz下的损耗控制在0.3dB/in以内,而黑孔工艺损耗超过1dB/in,无法满足需求。此外,5G PCB多为12-20层多层板,通孔纵横比常达12:1,仅沉铜工艺能实现均匀镀层。
2. 航空航天与医疗设备
航天电路板需耐受极端温度(-200℃至 + 200℃)与辐射环境,沉铜工艺的铜层热导率(401W/m・K)远高于碳粉膜(10-20W/m・K),可有效散热并维持电路稳定性。在医疗CT设备的高速数据传输板中,沉铜工艺的低延迟特性(信号传输速度达 0.6c)也是黑孔工艺无法企及的。
3. HDI 与半导体封装
高端HDI板(如手机主板)采用盲孔 / 埋孔结构,孔径仅50-100μm,沉铜工艺可实现孔壁镀层厚度均匀性±5%,而黑孔工艺在微孔径下碳粉分布不均,良率不足70%。半导体封装载板更依赖沉铜工艺的高可靠性,其失效概率可控制在1ppm 以下。
(二)黑孔工艺:绿色制造与成本敏感型场景的优选
1. 消费电子与家电
手机充电器、电视主板等双面板产品,对导电性能要求适中(频率 < 1GHz),黑孔工艺的成本优势(单平米成本降低15-20元)与环保特性(符合欧盟 RoHS认证)使其成为主流选择。以某品牌充电器PCB为例,采用黑孔工艺后年生产成本降低300万元,且废水排放减少8000吨。
2. 汽车电子与物联网
新能源汽车的电池管理系统(BMS)PCB需满足环保要求,黑孔工艺无甲醛排放的特点使其更易通过车企认证。在物联网传感器板中,小批量多品种的生产模式要求快速交付,黑孔工艺的短流程特性可将交期从7天缩短至3天,适配快速迭代需求。
3. 低端工业控制板
普通工业控制板(如 PLC 主板)工作频率低、结构简单,黑孔工艺的导电性能已能满足需求。某自动化设备厂商数据显示,采用黑孔工艺后,其PCB采购成本下降 25%,且因环保合规性提升,产品在欧洲市场的准入周期缩短40%。
五、技术发展趋势:环保与性能的融合创新
(一)黑孔工艺的突破方向
- 材料升级:纳米级碳粉(粒径<50nm)与石墨烯复合导电膜的研发,可将电阻率降低至 3μΩ・cm 以下,预计2026年实现10GHz 以下高频电路应用;
- 设备创新:脉冲静电吸附设备可提升深孔碳粉分布均匀性,预计2027年实现纵横比10:1孔的稳定处理;
- 工艺兼容:开发 “黑孔+局部沉铜” 混合工艺,在高频区域采用沉铜,其余区域采用黑孔,兼顾性能与成本。
(二)沉铜工艺的绿色转型
- 无甲醛药水商业化:醛类还原剂替代技术已进入中试阶段,新药水环保指标达欧盟REACH标准,预计2025年量产;
- 闭环废水处理:膜分离技术可将沉铜废水90%回用,水处理成本降至20 元/吨,某PCB龙头企业试点数据显示年节水15万吨;
- 智能化控制:AI算法实时监测药水成分,自动补充药剂,将药水更换周期从7天延长至21天,耗材成本降低60%。
(三)应用场景的边界拓展
- 中端市场融合:4-8层多层板将成为技术竞争焦点,黑孔工艺通过优化深孔处理能力,预计2028年在该领域占有率提升至40%;
- 特种 PCB 创新:在柔性PCB(FPC)与软硬结合板中,黑孔工艺的轻量化特性(碳粉膜密度仅为铜的 1/5)有望打开新应用空间;
- 可持续制造趋势:随着碳关税政策推进,黑孔工艺的低碳排放特性(单位产值碳排放较沉铜低70%)将获得更多政策倾斜。
六、结论:双轨技术驱动 PCB 行业升级
PCB黑孔工艺与沉铜工艺并非对立竞争,而是在不同维度推动行业进步 —— 沉铜工艺以卓越性能守护高端制造阵地,黑孔工艺以环保效率开拓绿色生产赛道。未来,随着材料科学与智能制造技术的突破,两者将在中端市场形成技术融合:沉铜工艺通过环保革新扩大应用边界,黑孔工艺通过性能提升渗透更高端领域。对于PCB制造商而言,依据产品定位选择适配技术,或布局混合工艺方案,将成为在产业变革中抢占先机的关键。
深泽多层电路作为行业领先者,始终关注孔金属化技术演进,可提供沉铜工艺高端HDI板、多层PCB板及高频高速PCB的全品类解决方案,助力客户在不同应用场景中实现性能与成本的最优平衡。
深泽多层电路是一家专业的PCB制造商,致力于高阶HDI、多层PCB、HDI打样、PCB打样、PCB快速打样、高频PCB、高速PCB、FPC、软硬结合板、SMT加工以及PCBA代工代料。他们提供一站式PCB及PCBA制造服务,不仅交期快速,而且价格具有竞争力。他们始终为客户提供高性价比和物美价廉的PCB及PCBA产品。
自2006年成立以来,一直致力于提供高阶HDI、多层PCB、HDI打样、PCB打样、PCB快速打样、高频PCB、高速PCB、FPC、软硬结合板、SMT加工以及PCBA代工代料等一站式制造服务。
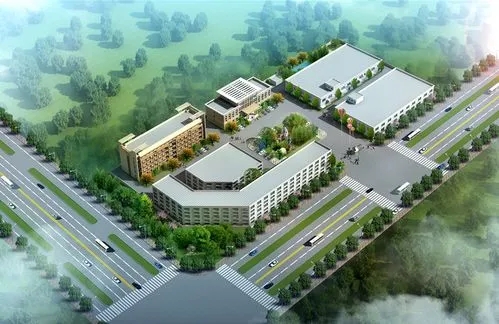