多层PCB制作难点及解决方法
一、概述
随着电子科技的迅速发展,高精密多层PCB已成为电子设备中的重要组成部分。这种PCB具有集成度高、精度高、密度高和层数多等特点,因此在制造过程中存在许多难点。本文将就高精密多层PCB制作过程中的难点进行深入分析,并提出相应的解决方法,希望此对您有所帮助。
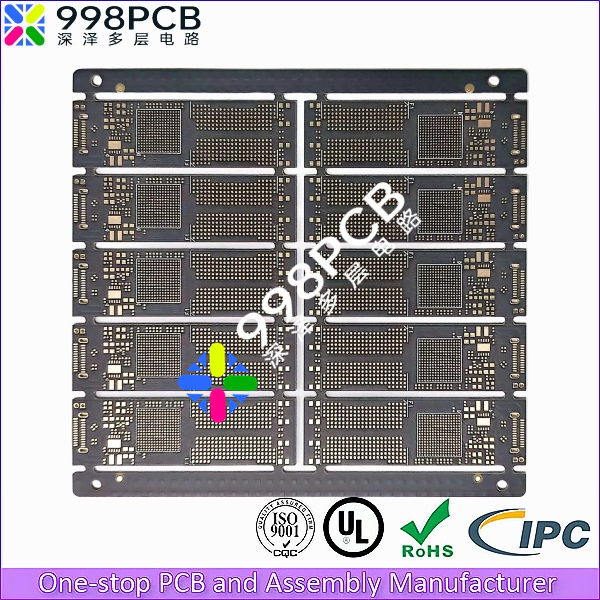
高精密U盘PCB
层数: 10L
板厚: 1.0mm
材质: S1000-2M Tg170
尺寸: 94.6*89.6mm/10
外层铜厚: 1OZ
内层铜厚: 0.5OZ
最小通孔: 0.15mm
线宽线距: 3/3mil
表面处理: 沉金1-2U”
特殊工艺: 树脂塞孔
ussd固态u盘电路板,SMI2320方案,广泛应用于高速数据备份、文件共享、移动办公等领域。
二、高精密多层PCB制作难点
1、设计复杂度高
高精密多层PCB的设计复杂度远高于传统的单、双面PCB板。其信号层数多,布线密度大,层间连接复杂,对设计人员的技能和经验要求极高。
此外,为了满足高速信号传输的需求,设计时还需考虑信号完整性、电磁兼容性等问题,这进一步增加了设计难度。
2、材料选择与控制
高精密多层PCB所使用的材料种类繁多,包括铜箔、绝缘层(PP)、覆盖层(油墨)等。这些材料的性能和质量直接影响到PCB的性能和质量。在选择材料时,需要考虑其物理、化学和电气性能,如导电性、绝缘性、耐热性、耐磨性等。
同时,由于多层PCB的结构特点,各层材料之间的匹配性和一致性也是需要考虑的重要因素。因此,材料的选择与控制是高精密多层PCB制作过程中的一大难点。
3、内层制作难度大
内层制作是高精密多层PCB的核心环节之一。由于布线密度大,内层制作时需要使用精细的线路刻画技术和可靠的层间连接技术。
此外,为了确保PCB的整体平整度和稳定性,还需要对每一层的材料和工艺进行严格控制。这不仅需要先进的设备和工艺技术,还需要严谨的质量控制体系。
同时,内层制作的难度也在于对细节的把握和对整体美观度的追求上。因此,内层制作是高精密多层PCB制作过程中的又一难点。
4、层间对准问题
多层PCB板由多达数4-64层的线路堆叠而成,每一层的材料、尺寸、线路布局等都需要精确匹配,才能确保信号的正确传输和电路的完整性。然而,在实际制作过程中,由于单元尺寸大、图形转换车间环境温湿度大、不同芯板不一致性造成的位错重叠等问题,使得多层PCB板的层间对准控制变得非常困难。因此,层间对准问题也是高精密多层PCB制作过程中的一个难点。
5、外层制作与表面处理
外层制作是高精密多层PCB的另一个核心环节。与内层制作相比,外层制作的难度主要体现在对细节的把握和对整体美观度的追求上。外层制作过程中,需要对表面处理工艺进行严格控制,以确保焊接质量和外观效果。此外,为了满足一些特殊需求,如防水、防尘等,还需要对外层进行特殊处理。因此,外层制作与表面处理是高精密多层PCB制作过程中的另一个难点。
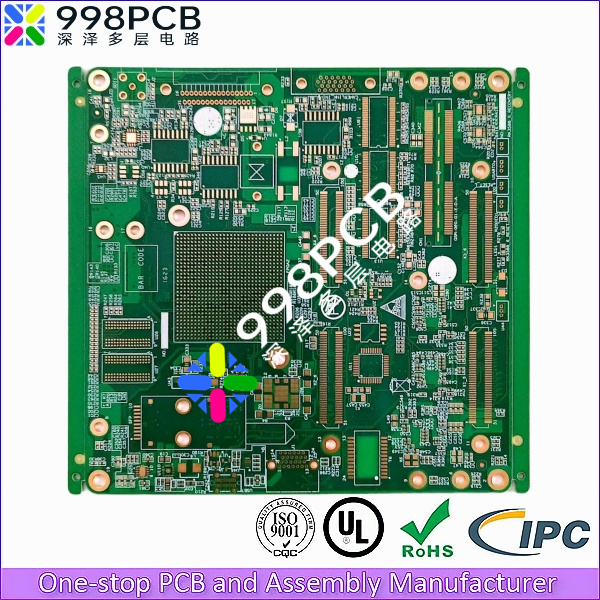
14层高精密PCB
层数: 14L
板材: FR4 S1000-2M
板厚: 1.6mm
拼板尺寸:130*120mm/1
外层铜厚: 1OZ
内层铜厚: 0.5OZ
最小孔径: 0.2mm
线宽线距: 3.5/3mil
表面处理: 沉金 1-2μ”
特殊工艺:背钻孔
高精密PCB,rk3588方案,可广泛应用于边缘计算、人工智能、工业控制、8K大屏、大数据分析、频采集、动环监测等领域。
三、解决方法
针对上述难点,可以采取以下解决方法:
1、提高设计人员的技能和经验水平
加强对设计人员的培训和技术交流,提高其技能和经验水平,使其能够更好地应对复杂的PCB设计任务。同时应积极引入先进的设计软件和工具,提高设计效率和准确性。让参与多层PCB的设计人员严格按照PCB行业的制程能力进行设计,以满足大多数PCB生产厂家的生产能力。
2、严格控制材料质量和工艺参数
对所使用的材料进行严格筛选和控制,确保其性能和质量符合要求。同时加强对工艺参数的控制,确保每一道工序的质量和稳定性。这可以通过引入先进的检测设备和加强质量管理体系来实现。对板材及菲林等生产原材料性能进行实际检测,如板材的膨胀系数、菲林膨胀系数进行实测。各种不同品牌的材料进行数据分析并建立数据,定期进行比对以保障原料的参数符合要求。
3、优化内层制作工艺
使用高精度线路制作设备和高性能材料,LDI曝光机、真空蚀刻机、等离子蚀刻机等,以提高线路的精细度和一致性。同时应定期对高精密设备进行校准和维护,确保设备的精度和稳定性。优化层间连接工艺,采用高温熔融PP、导电胶等连接方式,确保层间导电性能和机械连接的稳定性。在连接过程中,应严格控制温度、时间、压力等参数,避免对材料和结构产生不良影响。同时,应加强对内层制作过程中的质量控制,确保每一层的材料和工艺符合设计要求。
4、降低层间对准度偏差
采用高精度的切割、自动对位、层压设备,可以确保每一层的尺寸和位置精度,从而提高层间对准度。利用先进的设计和仿真软件,可以在制作前预测和纠正层间对准度误差,提高产品的制作质量和可靠性。建立严格的质量检测和控制体系,对每一道工序进行实时监控和检测,确保每一层的材料和工艺符合设计要求,从而提高层间对准度。
5、强化外层制作与表面处理技术
使用高精密钻孔、沉铜、电镀、线路制作设备,保证线路制作中的孔铜厚度、面铜厚度、线宽线距、蚀刻等的精度要求。加强表面处理工艺的控制,如喷锡、化学沉金、OSP等,以提高焊接质量和外观效果。在表面处理过程中,应严格控制化学成分、温度、时间等参数,确保表面处理的质量和稳定性。引入先进的光学检测技术和视觉识别系统,对外层制作进行实时监控和在线检测,确保产品质量的一致性和稳定性。这可以通过与检测设备制造商合作或自主研发来实现。