什么是PCB电镀塞孔
引言
在快速发展的电子工业中,电镀塞孔作为一种关键的PCB(Printed Circuit Board,印刷电路板)制造工艺,扮演着至关重要的角色。随着电子产品向“轻、薄、短、小”方向发展,PCB的集成度和密度不断提升,电镀塞孔技术以其独特的优势,成为解决高密度布线、提升电气性能和散热能力的重要手段。本文将从电镀塞孔的定义、原理、工艺流程、优势及应用等方面进行详细阐述。
一、PCB电镀塞孔的定义
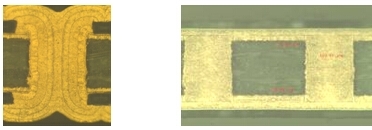
电镀塞孔,顾名思义,是指通过电镀工艺将金属(主要是铜)沉积在PCB板上的过孔内部,从而填满过孔并形成连续的金属层。这种技术主要用于解决PCB设计中过孔带来的电气连接、散热及可靠性问题。电镀塞孔不仅能够确保过孔内部具有良好的导电性,还能增强PCB的整体结构强度,提高产品的可靠性和使用寿命。
二、PCB电镀塞孔的原理
电镀塞孔的基本原理是利用电解作用,在含有金属离子的电解液中,通过电流的作用使金属离子在阴极(即PCB板上的过孔)表面还原成金属原子,并沉积在过孔内壁上,最终形成连续的金属层。这一过程中,电解液中的金属离子在电场作用下向阴极移动,并在阴极表面获得电子而还原成金属原子。随着电镀时间的延长,金属原子不断沉积,直至填满整个过孔。
三、电镀塞孔的工艺流程
电镀塞孔的工艺流程通常包括以下几个步骤:
- 钻孔:首先,在PCB基材上钻出所需的过孔。钻孔的精度和位置准确性对后续的电镀效果有着至关重要的影响。
- 去毛刺与清洗:钻孔后,过孔边缘可能会产生毛刺,需要通过去毛刺工艺进行处理。同时,对PCB板进行彻底清洗,以去除表面的油污、氧化物等杂质,确保电镀层与基材之间的良好结合。
- 沉铜:在过孔内壁上沉积一层薄薄的铜层,作为电镀的底层。这一步骤通常通过化学镀铜的方式实现,即在含有铜离子的溶液中,通过氧化还原反应在过孔内壁上形成一层均匀的铜层。
- 电镀铜:在沉铜的基础上,通过电镀工艺在过孔内部继续沉积铜层,直至填满整个过孔。电镀过程中需要控制电流密度、电镀时间、电解液温度等参数,以确保电镀层的均匀性和致密性。
- 去电镀液与清洗:电镀完成后,需要将PCB板从电镀液中取出,并进行彻底清洗,以去除表面残留的电镀液和杂质。
- 后续处理:根据需要进行研磨、抛光等后续处理,以确保电镀层的平整度和表面质量。同时,还可以进行镀金、镀镍等表面处理,以提高电镀层的耐腐蚀性和导电性。
四、电镀塞孔的优势
- 良好的导电性:电镀塞孔形成的金属层具有优良的导电性,能够确保PCB板上的电气信号传输畅通无阻。
- 增强结构强度:通过电镀填满过孔,可以增强PCB板的结构强度,提高产品的抗弯折、抗扭曲能力。
- 提高散热性能:电镀层具有良好的导热性,能够帮助PCB板上的热量快速散发出去,降低元件的工作温度,提高产品的稳定性和可靠性。
- 提升可靠性:电镀塞孔能够减少过孔内部的空气间隙和杂质,降低因氧化、腐蚀等原因导致的电气故障风险,提高产品的可靠性。
- 适应高密度布线:随着电子产品集成度的提高,PCB板上的布线密度越来越大。电镀塞孔技术能够解决高密度布线带来的电气连接和散热问题,满足电子产品对高性能、高可靠性的需求。
五、电镀塞孔的应用
电镀塞孔技术在电子工业中有着广泛的应用,特别是在以下领域:
- 高端服务器与数据中心:这些设备对PCB板的电气性能和散热性能要求极高。电镀塞孔技术能够确保PCB板上的电气信号传输畅通无阻,同时提高散热效率,满足高端服务器与数据中心对高性能、高可靠性的需求。
- 智能手机与平板电脑:随着智能手机和平板电脑的普及和性能提升,PCB板上的布线密度和元件数量不断增加。电镀塞孔技术能够解决高密度布线带来的电气连接和散热问题,提高产品的性能和可靠性。
- 汽车电子:汽车电子系统对PCB板的可靠性和耐久性要求极高。电镀塞孔技术能够增强PCB板的结构强度和抗腐蚀性能,确保汽车电子系统在恶劣环境下稳定工作。
- 航空航天:航空航天领域对电子产品的重量、体积和性能要求极为严格。电镀塞孔技术能够在保证电气性能的前提下减轻PCB板的重量和体积,提高航空航天设备的综合性能。
六、结论
电镀塞孔技术作为PCB制造中的一项关键技术,对于提升电子产品的电气性能、散热性能和可靠性具有重要意义。通过不断优化工艺流程、研发新材料和新工艺以及实现自动化和智能化生产,电镀塞孔技术将不断满足电子产品对高性能、高可靠性和环保性的需求。未来,随着电子技术的持续发展和市场需求的变化,电镀塞孔技术将继续发挥重要作用,为电子工业的发展贡献更多力量。
深泽多层电路是一家专业的PCB制造商,致力于高阶HDI、多层PCB、HDI打样、PCB打样、PCB快速打样、高频PCB、高速PCB、FPC、软硬结合板、SMT加工以及PCBA代工代料。他们提供一站式PCB及PCBA制造服务,不仅交期快速,而且价格具有竞争力。他们始终为客户提供高性价比和物美价廉的PCB及PCBA产品。
自2006年成立以来,一直致力于提供高阶HDI、多层PCB、HDI打样、PCB打样、PCB快速打样、高频PCB、高速PCB、FPC、软硬结合板、SMT加工以及PCBA代工代料等一站式制造服务。
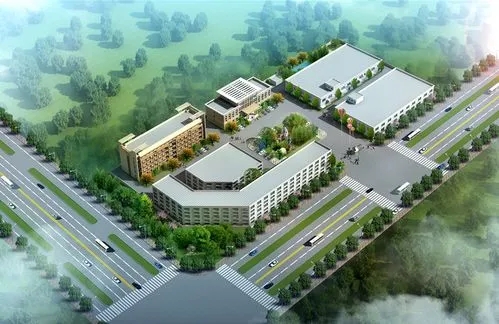