什么是PCB的盘中孔
在现代电子制造业中,印刷电路板(PCB)作为电子元器件的载体与连接桥梁,其设计与制造技术直接关系到电子产品的性能、可靠性及制造成本。在众多PCB设计元素中,盘中孔(Via-in-Pad, VIP)作为一种特殊而重要的设计,因其独特的布局和功能,在提升电路板集成度、优化电气性能及散热能力等方面展现出了显著优势。本文将从盘中孔的定义、应用场景、特点、制造工艺流程及优缺点等五个方面,深入探讨这一关键技术。
一、PCB的盘中孔定义
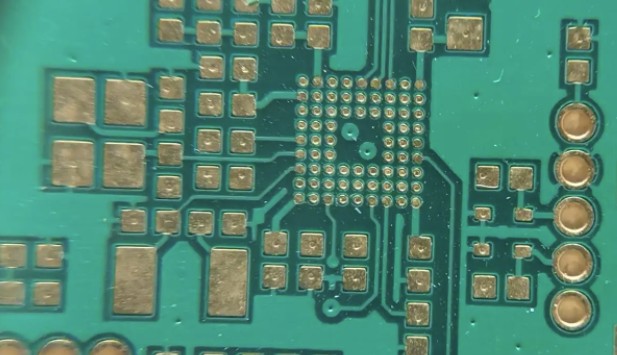
盘中孔,顾名思义,是指将过孔(Via)直接设计在PCB板上的BGA或贴片焊盘(Pad)内部或边缘的一种特殊结构。盘中孔的设计初衷主要是为了解决高密度集成电路板中空间有限的问题。随着电子产品向小型化、轻薄化方向发展,PCB板上的元件密度和布线复杂度不断增加,传统的过孔布局方式往往难以满足设计要求。而盘中孔的设计则通过合理利用焊盘内部或边缘的空间,实现了层间连接的紧凑布局,有效提升了电路板的集成度和布线灵活性。
二、盘中孔的应用场景
1. 高密度电路设计
随着电子产品的微型化和功能多样化,PCB上的元件密度越来越高,布线空间变得极为有限。盘中孔设计允许在焊盘内部或边缘布置过孔,从而在不增加PCB面积的情况下,实现更多的层间连接,有效提升了电路板的集成度和布线灵活性。
2. 散热管理
对于大功率、高发热量的元器件(如CPU、GPU等),散热问题是设计的关键。通过在焊盘上设计盘中孔,可以增加元器件与PCB基板之间的热传导路径,提高散热效率。此外,部分设计中还会在盘中孔内填充导热材料,进一步增强散热效果。
3. 机械固定与支撑
在某些应用场景下,需要对PCB板上的元器件进行机械固定,以确保其在振动、冲击等恶劣环境下的稳定性。通过在焊盘上打孔并安装螺丝或其他紧固件,可以实现元器件的牢固固定。同时,这些盘中孔还能作为PCB板的支撑结构,增强整体机械强度。
4. 特定元件安装
部分特殊元件(如BGA封装芯片)的底部焊球需要与PCB板上的焊盘直接连接。为了确保连接的可靠性和稳定性,设计中可能会采用盘中孔结构来提供额外的支撑和定位功能。
三、盘中孔的特点
1. 节省空间
盘中孔设计充分利用了焊盘内部或边缘的空间,实现了层间连接的紧凑布局,从而节省了PCB上的布线空间,提高了集成度。
2. 增强散热
通过增加热传导路径和可选的导热材料填充,盘中孔设计显著提升了PCB板的散热性能,有助于降低元器件的工作温度,延长使用寿命。
3. 机械支撑
作为PCB板的支撑结构之一,盘中孔增强了电路板的整体机械强度,提高了其在各种环境下的稳定性和可靠性。
4. 布线灵活性
盘中孔的设计使得布线更加灵活多样,可以在有限的空间内实现复杂的电气连接,满足高性能电路的需求。
四、盘中孔的制造工艺流程
1. 钻孔
采用机械钻孔或激光钻孔技术,在PCB板上钻出所需的孔位。这一步需要严格控制钻孔精度和孔径大小,以确保后续工艺的顺利进行。
2. 镀铜
为了增强孔的导电性和机械强度(尽管VIP本身不导电,但镀铜为后续工艺做准备),对孔壁进行电镀铜处理。镀铜层需均匀且致密,以满足后续工艺要求。
4. 封堵与填孔(针对VIP)
对于VIP设计,需要在电镀铜后使用特定的材料(如树脂)对孔进行封堵或填孔处理。这一步是为了防止后续工艺中的化学物质进入孔内,影响焊盘质量和电气性能。同时,填孔处理还能增强VIP的机械支撑能力。
5. 焊盘制作
在封堵或填孔完成后,进行焊盘制作。这通常包括涂覆感光阻焊层、曝光、显影、电镀铜等步骤,最终在PCB板上形成符合设计要求的焊盘。
五、盘中孔的优缺点
优点
- 节省空间:盘中孔设计显著减少了PCB板上对额外空间的需求,使得在高密度电子产品的设计中能够容纳更多的元件和更复杂的布线,提高了设计的集成度和紧凑性。
- 增强散热:通过在焊盘内部或边缘设置过孔,增加了元器件与PCB基板之间的热传导路径,有效提升了散热效率。这对于需要高效散热的电子设备尤为重要,如高性能计算机、服务器和高端消费电子设备等。
- 提高机械强度:盘中孔可以作为PCB板的机械支撑点,特别是在安装大型或重型元器件时,能够增强PCB板的整体机械强度,减少因振动、冲击等外力作用导致的损坏风险。
- 布线灵活性:盘中孔设计提供了额外的布线通道,使得在有限的PCB板面积上实现更复杂的电气连接成为可能,满足了现代电子产品对高集成度和高性能的需求。
- 便于安装与固定:对于需要精确安装和固定的元器件(如BGA封装芯片),盘中孔设计提供了额外的定位点和固定点,有助于实现元器件的精确安装和稳固固定。
缺点
- 制造工艺复杂:相比传统的PCB设计,盘中孔制造工艺更为复杂,需要更精确的钻孔、填孔和电镀等步骤。这增加了制造成本和工艺难度,对制造设备和工艺控制提出了更高的要求。
- 可靠性挑战:盘中孔设计可能导致焊盘与过孔之间的连接可靠性问题。如果填孔材料选择不当或工艺控制不严格,可能会出现填孔不饱满、裂纹或脱落等问题,影响PCB板的电气性能和可靠性。
- 散热不均:虽然盘中孔设计有助于提升散热效率,但在某些情况下也可能导致散热不均的问题。如果填孔材料导热性能不佳或散热路径设计不合理,可能会造成局部过热现象,影响元器件的性能和寿命。
- 设计限制:盘中孔设计受到PCB板厚度、孔径大小、镀铜层厚度等多种因素的限制。在设计过程中需要综合考虑这些因素,以确保设计的合理性和可行性。此外,由于制造工艺的复杂性,盘中孔设计可能会增加设计周期和成本。
- 维修困难:一旦PCB板上的元器件出现故障需要更换或维修时,盘中孔设计可能会增加维修难度。由于焊盘内部或边缘存在过孔结构,可能需要采用特殊的维修工具和工艺才能进行修复或更换。
综上所述,PCB的盘中孔设计在提升集成度、优化散热性能、增强机械强度等方面具有显著优势,但同时也面临着制造工艺复杂、可靠性挑战、散热不均、设计限制和维修困难等缺点。因此,在实际应用中需要根据具体需求和条件进行权衡和选择,以充分利用其优势并尽量避免其缺点对产品性能和可靠性的影响。