生益S1000-2M板材介绍
一、生益S1000-2M板材概述
生益S1000-2M板材属于高性能的FR-4玻纤板材类别,由生益科技精心研发制造。它以玻璃纤维布作为增强材料,环氧树脂为基体,通过先进且严谨的工艺复合而成。该板材具备高玻璃化转变温度(Tg),其Tg值达到180℃,在中高Tg板材领域表现卓越,这一特性使其在高温环境下能维持良好的性能,满足了众多对温度稳定性要求严苛的应用场景。作为一种被广泛认可的优质基板材料,S1000-2M板材常用于制作高阶HDI及高精密多层印刷电路板(PCB),为各类高端电子设备的稳定运行提供坚实基础,在电子电路行业占据重要地位。
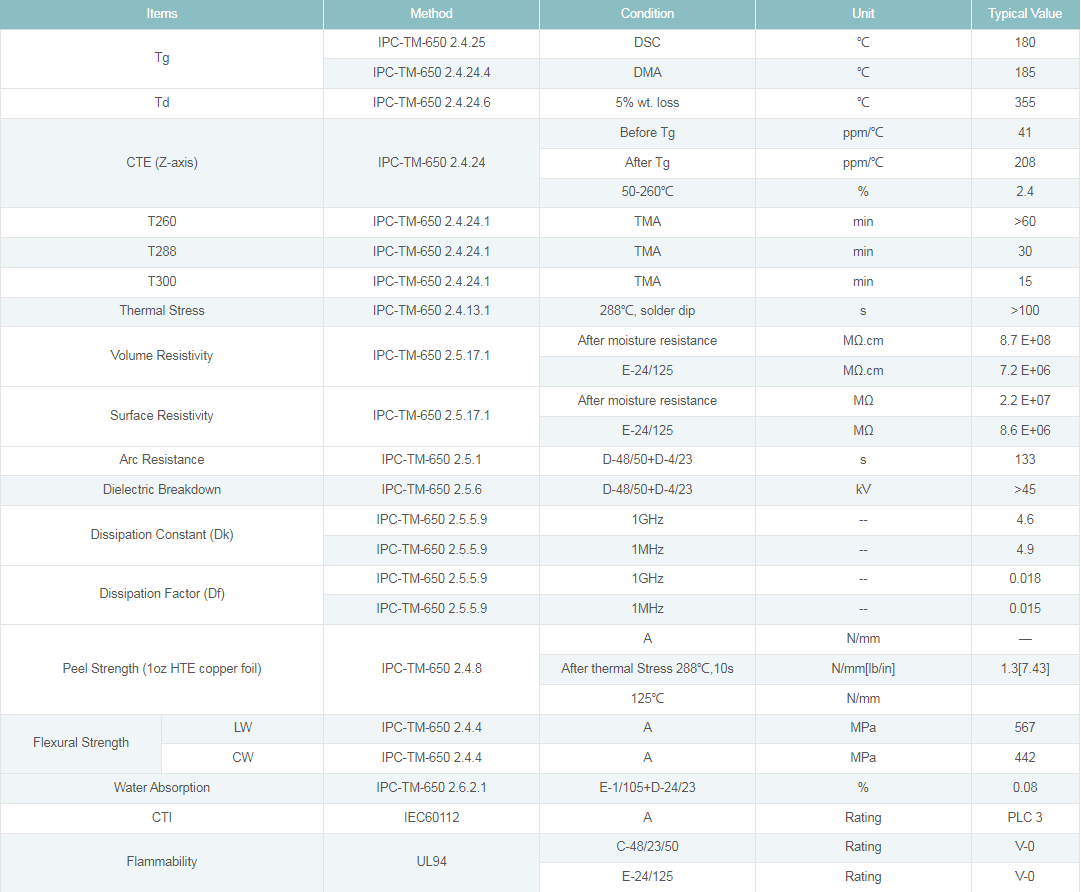
二、产品性能介绍
(一)电气性能
- 绝缘性能:S1000-2M板材拥有极高的绝缘电阻,在IPC-TM-6502.5.17.1标准下,经过耐湿处理后,其体积电阻率可达8.7×10⁸MΩ・cm,表面电阻率为2.2×10⁷MΩ。如此出色的绝缘性能,能有效阻止电流泄漏,确保电路中信号传输的准确性与稳定性,避免因漏电导致的信号干扰或电路故障。无论是在日常电子设备,还是对电气性能要求极为苛刻的工业控制、医疗设备等领域,都能可靠地保障电路正常工作。
- 介电性能:在1GHz频率下,板材的介电常数(Dk)为3.6-4.6,介电损耗因子(Df)为0.018。适中且稳定的介电常数,使得信号在传输过程中能够以较低的损耗传播,极大地提升了信号的传输速度与质量。特别是在当下高速发展的5G通信、高速数据传输等领域,S1000-2M板材低信号损耗的特性,可显著减少信号失真与延迟,保证数据的快速、准确传输,满足高频高速信号处理的需求。
- 耐电压性能:它具备良好的耐电压能力,能够承受较高的电压而不发生击穿现象。在实际应用中,这为电子设备在高电压环境下的安全稳定运行提供了可靠保障。例如在电源供应设备、高压电气控制电路等场景中,S1000-2M板材可有效避免因电压过高导致的电气事故,增强了产品的电气安全性与可靠性。
(二)热性能
- 玻璃化转变温度(Tg):如前文所述,S1000-2M板材的Tg值高达180℃,属于高Tg板材。这意味着在达到180℃之前,板材能保持良好的物理和化学性能,不会因温度升高而出现软化、变形等问题。在电子设备运行时,尤其是一些发热量大的部件附近的PCB,如计算机CPU散热器下方的主板区域、汽车发动机控制单元(ECU)内部的电路板等,S1000-2M板材能够稳定工作,确保电路的可靠性,避免因温度影响导致设备故障。
- 热膨胀系数:该板材具有较低的热膨胀系数,在IPC-TM-6502.4.24标准下,Z轴方向热膨胀系数(CTE)在Tg之前为41ppm/℃。在温度变化过程中,板材尺寸变化微小,这对于多层PCB的制作和使用极为关键。它能有效降低因热胀冷缩产生的层间应力,减少PCB出现分层、开裂等问题的风险,提高了产品的长期可靠性与稳定性,使电子设备能够在不同温度环境下长时间稳定运行。
- 热传导率:尽管S1000-2M板材主要作为绝缘材料使用,但具备一定的热传导能力,能够将电子元件产生的热量及时传导出去,辅助散热系统工作。这有助于降低电子设备的整体温度,提高电子元件的工作效率和使用寿命。在一些对散热要求较高的电子产品,如高性能显卡、大功率服务器等的PCB中,S1000-2M板材的热传导性能可协同散热风扇、散热片等,更好地控制设备温度,确保其高性能运行。
(三)机械性能
- 弯曲强度:S1000-2M板材具有较高的弯曲强度,在IPC-TM-6502.4.4标准下,达到567MPa。这使其在一定程度上能够承受弯曲而不断裂,在电子产品的安装和使用过程中,即使PCB受到一定外力作用,如在一些可穿戴设备、折叠式电子设备中,需要对PCB进行弯折安装,S1000-2M板材可确保PCB在弯折后依然能正常工作,保证了产品结构设计的灵活性与可靠性。
- 拉伸强度:其拉伸强度同样出色,能够抵抗一定的拉伸力。在电子产品组装时,可能会对PCB施加拉伸力,例如在插拔连接部件、安装固定螺丝时,S1000-2M板材制作的PCB能够承受这些力而不被拉断,保障了产品组装过程中的完整性与质量,避免因PCB损坏导致设备故障。
- 硬度:板材具有合适的硬度,既能在加工过程中保持形状稳定,不易变形,又能在使用中抵抗外界的刮擦和碰撞,保护PCB上的电路不受损坏。在消费电子产品,如手机、平板电脑等日常频繁使用且易受外力冲击的设备中,S1000-2M板材的硬度特性可有效保护内部PCB,延长设备使用寿命。
三、产品特点
(一)卓越的抗CAF能力
CAF(ConductiveAnodicFilament)即导电阳极丝,是影响电路板长期可靠性的关键因素之一。在高湿度和电场的共同作用下,电路板中的金属离子容易迁移形成细丝状导电通路,进而引发电路短路等严重故障。S1000-2M板材通过独特的配方设计和先进的制造工艺,构建了稳定且致密的内部分子结构,能够有效阻止金属离子的迁移,显著降低CAF发生的概率。这使得使用该板材制作的PCB在恶劣环境条件下,如高湿度的工业环境、沿海地区的户外设备以及热带高温高湿气候环境中的电子设备等,也能长时间稳定运行,大幅减少设备的维护成本和故障率,提高了电子产品的可靠性与使用寿命。
(二)无铅兼容
随着全球环保意识的不断增强以及环保法规的日益严格,无铅焊接工艺已成为电子行业的主流趋势。S1000-2M板材完全适应无铅焊接工艺要求,符合环保标准。在无铅焊接过程中,板材能够承受高温而不发生变形、分层等问题,同时保持良好的焊接性能,确保电子元件与PCB之间的连接牢固可靠。这为电子制造商生产符合环保要求的绿色电子产品提供了有力支持,推动了整个电子行业向环保、可持续方向发展。
(三)超低吸水率
在电子产品的使用过程中,尤其是在潮湿环境下,PCB板材的吸水率对其性能有着重要影响。S1000-2M板材具有极低的吸水率,能够在湿润环境中保持性能稳定。当板材吸收过多水分时,可能会导致电气性能下降,如绝缘电阻降低、介电常数变化等,还可能引发CAF等问题。而S1000-2M板材由于吸水率低,可有效避免这些问题的发生,延长了电路板的使用寿命。在一些户外电子产品、卫浴设备中的电子部件、水下监测设备等应用场景中,S1000-2M板材的低吸水率优势得以充分体现,确保设备在潮湿环境下可靠运行。
(四)出色的热可靠性
综合其热性能特点,S1000-2M板材在高温环境下仍能保持稳定的电气性能、机械性能和化学性能,展现出出色的热可靠性。无论是在电子产品正常运行时产生的热量,还是在一些极端高温环境下,如汽车发动机舱内(温度可达100℃以上)、工业高温炉旁的电子设备(工作温度可能超过150℃)等,S1000-2M板材制作的PCB都能可靠工作,保证设备的正常运行,为电子产品在高温环境下的应用提供了坚实保障,拓宽了电子设备的使用环境范围。
(五)优良的通孔可靠性
在PCB制作过程中,通孔是连接不同层电路的关键结构,其可靠性直接影响电路板的整体性能。S1000-2M板材具有优良的通孔可靠性,在钻孔、金属化等工艺过程中,能够保证通孔的质量,使通孔与板材之间形成良好的结合力。这确保了电流在不同层之间的顺畅传输,提高了电路板的整体性能和耐用性。在多层PCB中,往往存在大量的通孔,S1000-2M板材的这一特点可有效减少因通孔问题导致的电路故障,提高产品的良品率,降低生产成本,提升生产效率。
(六)出色的机械加工性能
S1000-2M板材在机械加工方面表现出色,易于进行钻孔、铣削、切割等加工操作。在钻孔过程中,能够保证孔壁光滑、孔径精度高,减少钻头磨损,提高钻孔效率;铣削时,可加工出高精度的外形和精细结构,满足复杂PCB设计的要求。这使得电子制造商能够更加高效地将其加工成各种形状和规格的PCB,提高生产效率,同时保证产品质量的稳定性和一致性,降低加工成本,增强产品在市场上的竞争力。
四、加工指南
(一)钻孔
- 刀具选择:鉴于S1000-2M板材具有一定硬度,钻孔时需选用优质刀具。硬质合金钻头是理想选择,其高硬度和良好的耐磨性可有效提高钻孔效率与质量,减少钻头磨损。对于普通孔径钻孔,可选用含钴硬质合金钻头;对于高精度、小孔径钻孔,整体硬质合金微钻更为合适,如加工0.25mm以下小孔径时,整体硬质合金微钻能保证钻孔精度和孔壁质量。
- 钻孔参数:合理的钻孔参数对保证孔质量至关重要。转速通常需根据钻头直径和板材厚度调整,一般在20000-60000转/分钟之间。例如,使用3mm直径钻头加工1.6mm厚板材时,转速可设置为35000转/分钟左右。进给速度不宜过快,以免造成孔壁粗糙、毛刺过多等问题,一般在0.1-0.5毫米/转之间。同时,要注意控制钻孔温度,可采用冷却液或风冷方式冷却,如使用专用的PCB钻孔冷却液,通过循环系统将冷却液喷洒到钻孔部位,带走热量,防止板材因过热而损坏。
- 注意事项:钻孔前,务必确保板材固定牢固,可使用专业的板材固定夹具,避免钻孔过程中板材位移影响钻孔精度。对于多层板,要严格控制不同层之间的对准精度,采用高精度的定位系统,防止通孔错位。此外,需定期检查钻头磨损情况,一般每钻孔500-1000次检查一次,及时更换磨损严重的钻头,以保证钻孔质量的一致性。
(二)铣削
- 铣刀选择:铣削S1000-2M板材应选用锋利铣刀,高速钢铣刀或硬质合金铣刀均可。对于外形加工等精度要求较高的铣削操作,硬质合金铣刀能更好地保证加工尺寸精度和表面质量。对于复杂形状铣削,可选用专用成型铣刀,如加工带有异形凹槽、凸起等结构的PCB时,使用定制的成型铣刀可一次性加工出所需形状,提高加工效率和精度。
- 铣削参数:铣削速度一般在8000-20000转/分钟之间,如加工一般精度的PCB外形时,可设置为12000转/分钟。进给速度根据铣刀直径和加工要求而定,通常在500-2000毫米/分钟之间。切削深度不宜过大,以免造成板材分层或崩边等问题,一般在0.5-2毫米之间。例如,使用6mm直径铣刀进行外形铣削时,切削深度可控制在1mm左右。
- 注意事项:铣削过程中,要保持铣刀锋利度,定期对铣刀进行刃磨或更换,一般每铣削8-10小时进行一次刃磨,当铣刀磨损超过一定限度(如刀刃磨损量达到0.2mm)时及时更换。同时,要注意板材装夹方式,采用合适的装夹夹具,确保板材在铣削过程中稳定可靠,避免因装夹不牢导致板材移动或振动,影响加工质量。对于薄壁结构或精细部位铣削,要降低铣削速度和进给速度,如铣削0.5mm以下薄壁结构时,铣削速度可降至6000转/分钟,进给速度降至300毫米/分钟,小心操作,避免因铣削力过大损坏板材。
(三)表面处理
- 沉金:沉金是常见的PCB表面处理方式,可提高PCB可焊性和电气性能。对S1000-2M板材进行沉金处理时,要严格控制工艺参数。金盐浓度一般控制在3-5g/L,温度保持在85-95℃,时间为10-15分钟,以保证沉金层厚度均匀、附着力良好,一般沉金层厚度在0.05-0.1微米之间。在沉金过程中,要定期检测金盐浓度、温度等参数,确保工艺稳定性。
- 沉银:沉银处理能为PCB提供良好焊接性能和抗氧化性能。沉银时,要精确控制银离子浓度在2-3g/L,pH值保持在4.5-5.5之间,通过调整这些参数确保沉银层质量。沉银层厚度一般在0.1-0.3微米之间。同时,要注意沉银后的清洗工艺,使用去离子水进行多次清洗,去除表面残留的化学药剂,防止对后续焊接和电气性能产生影响。
- 喷锡:喷锡是经济实用的表面处理方式。对于S1000-2M板材,喷锡时锡液温度需控制在250-270℃,喷射压力为0.2-0.3MPa,使锡层均匀覆盖在PCB表面,厚度一般在0.8-2微米之间。喷锡后,要进行清洗和检验,使用专用清洗剂去除表面残留助焊剂等杂质,通过外观检查、厚度测量等手段确保喷锡质量符合要求。
五、应用领域
(一)通信设备领域
在5G通信基站中,S1000-2M板材凭借其出色的电气性能,能够满足高速率、大容量数据传输对PCB的严格要求。其低介电常数和低介电损耗特性,可有效减少信号传输过程中的损耗和延迟,确保基站设备间通信信号的快速、准确传输,提升通信质量和网络覆盖范围。在通信交换机、路由器等设备中,该板材的高可靠性和稳定性,可保证设备在长时间、高负荷运行下稳定工作,减少故障发生,为通信网络的稳定运行提供坚实基础。
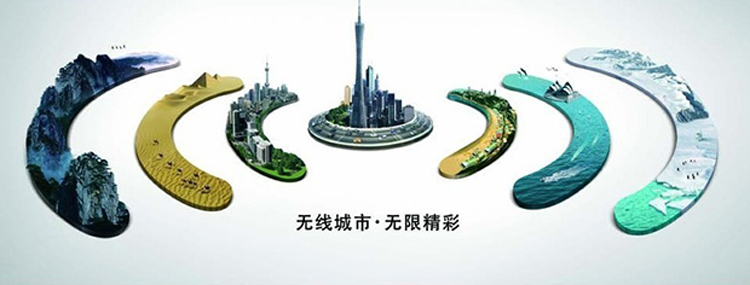
(二)计算机与服务器领域
计算机主板作为计算机的核心部件,对PCB性能要求极高。S1000-2M板材的高热可靠性和优良电气性能,能够保证计算机在长时间高负荷运行过程中,主板稳定工作,数据传输快速准确。在服务器领域,尤其是高性能计算服务器,其运行时会产生大量热量,且对数据处理速度和稳定性要求极为苛刻。S1000-2M板材的高Tg值和低膨胀系数,使其能在高温环境下保持稳定,有效降低因热胀冷缩导致的故障风险,确保服务器高效、稳定运行,满足大数据存储、云计算等业务对服务器性能的严格要求。
(三)汽车电子领域
汽车电子系统涵盖发动机控制系统、车载娱乐系统、安全系统等多个部分,工作环境复杂,对PCB可靠性要求极高。在发动机控制系统中,S1000-2M板材可在高温(发动机舱内温度可超100℃)、高振动等恶劣环境下,确保发动机控制信号准确传输和系统稳定运行,保障汽车的动力性能和安全性能。在车载娱乐系统和自动驾驶辅助系统中,该板材的抗干扰能力和电气性能,可保证信息娱乐功能的流畅运行以及传感器数据的准确处理,提升驾驶体验和行车安全性。
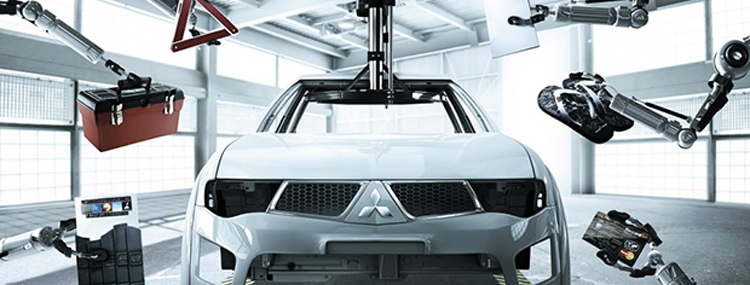
(四)工业控制领域
工业自动化设备、机器人控制等工业领域的工作环境往往存在高温、高湿度、强电磁干扰等情况。S1000-2M板材凭借其出色的综合性能,可确保工业设备中的PCB稳定工作。例如在工业自动化生产线中的控制器、传感器电路板中,该板材能够抵抗恶劣环境影响,保证设备的自动化控制和监测功能正常运行,提高工业生产的可靠性和效率,减少因设备故障导致的生产停滞和损失。
(五)医疗设备领域
医疗检测设备、分析仪器等对PCB的性能和可靠性要求极为严格。S1000-2M板材的高精度信号传输能力和高稳定性,可满足医疗设备对数据采集、处理和传输的准确性要求。在医学影像设备,如CT、MRI等中,使用该板材制作的PCB能够确保图像信号的准确采集和传输,为医生提供清晰、准确的诊断图像,助力医疗诊断的准确性和可靠性,对保障患者的健康和生命安全具有重要意义。